The Great Berkhamstead Gas Light and Coke Company
by
Tony Statham,
reproduced by kind permission of the author.
We are all familiar with the phrase “fossil fuels” applied to oil,
gas and coal and know that most of our utility needs are met from
these commodities. Recent price rises in all these items have
been very much in the news over the past year and even with the
subsequent fall in the oil price, remain a topic of everyday
conversation. Most of us probably take fossil fuels for
granted and I am sure few people consider the origins of their
electricity when they flick a switch to power up a computer,
electric kettle or all their other domestic appliances. Gas is
perhaps a little more “hands on” as the user has to ignite the
material unless it is used in a heating boiler where this is
typically done automatically. However, most gas customers
again assume that the pipe laid to their house or premises somehow
arrives by magic without too much concern for its origin.
While coal, per se, has been known as a fuel for thousands of years,
as early as the 17th
century, scientists were discovering that a “wild spirit” escaped
from wood or coal if these were heated. The Flemish scientist,
Jan Baptista van Helmont (1577-1644) thought this substance
“differed little from the chaos of the ancients” and named it gas in
his Origins of Medicine (c. 1609). Several others
experimented with the “Spirit of the Coal” and in England, William
Murdoch (later Murdock) (1754-1839) and a partner of James Watt, is
reputed to have heated coal in his mother’s teapot to produce gas.
He developed new ways of making, purifying and storing gas and by
1792 had installed gas lighting in his house at Redruth.
Further installations followed in various premises and other
demonstrations and installations were established in France and the
United States. It is however generally recognised that the
first commercial gas works was that built by the London and
Westminster Gas Light and Coke Company in Great Peter Street in 1812
laying wooden pipes to illuminate Westminster Bridge the following
year. The all too familiar practice of digging up streets to
lay gas piping required legislation and to some extent this hindered
the development of street lighting and gas for domestic use.
Nevertheless, by the 1850s every small to medium sized town and city
had a gas plant to provide for street lighting. In the 1860s
(and the remainder of the 19th century) several other advances were
made in the production and use of gas. Perhaps one of the most
important was the introduction of the gas mantle, a somewhat fragile
impregnated mesh, which allowed the gaslight to burn with a much
brighter and more even flame. An ordinary gas flame is similar
in illumination to a single candle whereas the application of a
mantle produces something akin to a 100-watt electric light bulb.
This development naturally had a dramatic effect on industry and
domestic life enabling night-shift work to expand, encourage more
people to read and write and render public streets and spaces safer
after dark. Towards the end of 19th century, the invention of
the gas meter played an important role in selling “town gas” to
domestic and commercial customers for lighting and subsequently
heating and cooking appliances.
The Great Berkhamstead Gas Light and Coke Company built the first
gas works in Berkhamsted in 1849 at the lower end of The Wilderness,
effectively where the Water Lane car park extends behind Tesco; the
manager of the works lived in Adelbert House, which remains today on
the corner of Mill Street. At this time the Parish Vestry
oversaw the development of public health, relief for the poor and
other services in the town. However, the funds to build the
gas works were raised by public subscription and the company started
with a capital of £2000 comprising 400 shares of £5 each. This
was sufficient to establish the works (£1800), the initial service
pipes (£3-13-1ld) and install street lighting. The Vestry
consequently only had to pay for the gas itself and any maintenance
came from the rates.
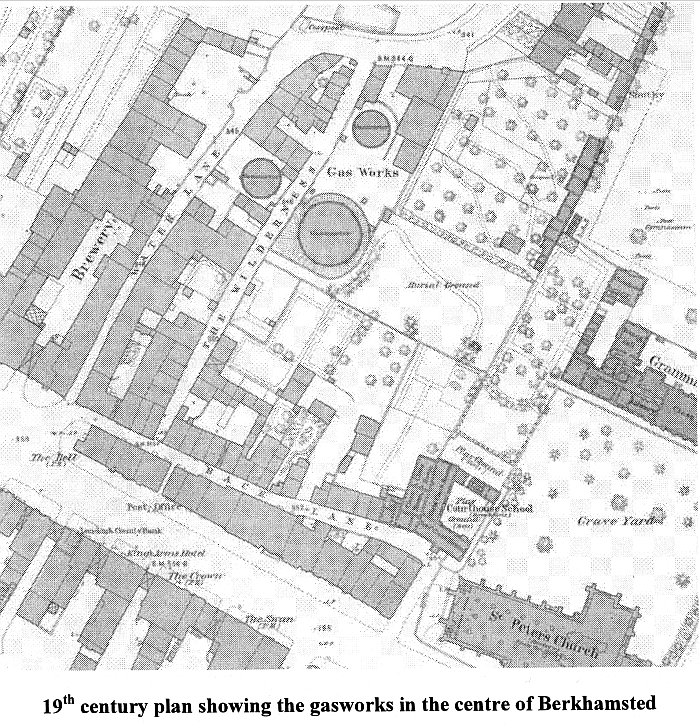
The first Trustees of the company were R. A. Smith Dorrien (of
Haresfoot) and Mr T. P. Halsey MP (of Berkhamsted Hall). The
first chairman was the Hon. Col. J. Finch (of Berkhamsted Place) and
the directors included J. E. Lane of Lane’s Nurseries. The
first year of operations yielded an income of £242-12-2d from the
sale of gas while by-products such as coke and tar yielded
£35-19-10d. The company’s records show that the cost of coal
in the first year was £67-0-6d and that a surplus in excess of £150
allowed a dividend of 5% to be paid. It is recorded with a
note of disappointment that the Town Inspectors failed to pay their
first gas bill (£74-5-0d) for public lighting. However the
directors were sufficiently optimistic to reduce the price of gas
after the first year from 8/4d to 7/6d per 1000 cu. ft. This
level of generosity proved so popular in increasing the customer
base that the price ultimately fell to just 4/9d per 1000 cu. ft. by
1882. Ultimately, the persistent increase in coal prices put a
stop to this practice and the company records suggest that the gas
price stabilised at around 5/- per 1000 cu. ft.
The generation of “coal gas” as it was sometimes known, naturally
depended on a regular supply of coal and at the inception of the
works, this fuel was brought by canal boat although the railway had
reached Berkhamsted by 1837. However it was not long before
rail freight became a more viable alternative and soon coal was
being delivered by rail with the return wagons taking tar and other
by-products from the gasworks, back to London.
The annual reports and minutes of company meetings from 1849 to
1905, which are held in the Museum Store, provide detailed accounts
of the various maintenance and expansion works that were deemed
appropriate as the supply of gas extended to the boundaries of the
town. The original three iron retorts were expanded to five in
1852 and then replaced by brick ovens in 1855. This year also
witnessed the cancellation of supply contracts to the town
inspectors and the station in favour of meters being installed.
This apparently allowed the town to reduce street lighting by some
25%. In 1856, additional land was purchased for a second
gasholder and in 1857 the height of the chimney to the “furnace” was
raised “to carry off the vapour from the purifiers and thereby
remove a nuisance which was threatening the very existence of the
works”. A new six-inch main was laid to the High Street in
1858 (replacing a three-inch one) and new pipes were laid to Manor
Street and Ravens Lane. By 1860, over one million cubic feet
of gas were being generated and in 1861, Thomas Curtis took over the
chairmanship of the company.
Throughout this period the financial profile of the company grew
substantially, new shares were issued, profits were raised and the
dividends were increased. The new capital and higher levels of
income allowed continued expansion of the works and the network of
service pipes, and in 1868 a second site in Water Lane was acquired
to erect another gasholder. In 1873 it was decided to change
the company’s bankers who had been Messrs Butcher and Co. in Tring
to the more convenient London and County Bank in Berkhamsted High
Street.
In 1886 additional land between the works and the River Bulbourne
(owned by Earl Brownlow) was earmarked for future expansion. However
in 1892 the Sanitary Authority had instituted proceedings for an
“alleged nuisance” from the works and by 1903 the governors of the
neighbouring Grammar School expressed a strong desire for the
removal of the works altogether. This is perhaps not so surprising
given the relatively anti-social environment of a gas producing
plant in the centre of a market town. Apart from the disadvantages
of coal-dust and the manufacturing plant itself, various waste
products inevitably would have contaminated the site. To be fair,
the area around the Wilderness at the end of 19th century was not
especially salubrious but the gasworks would certainly have been an
added blight on the town centre. Lord Brownlow again provided a
solution by offering a totally new site off Billet Lane.
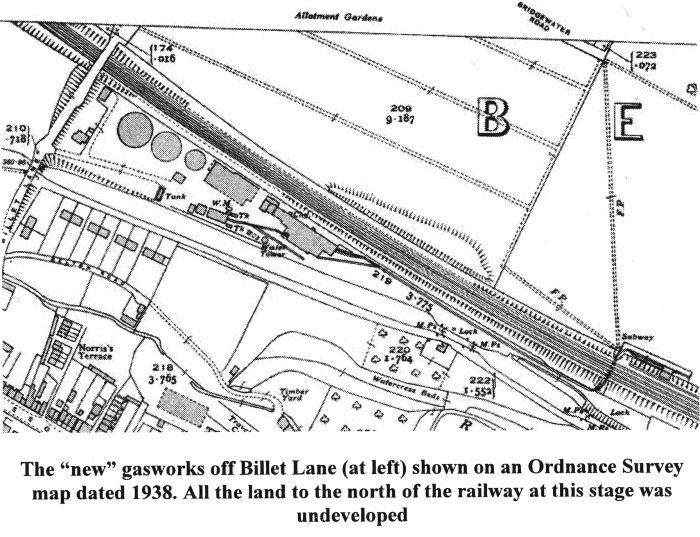
The new site lay between the canal and the railway and is now the
River Park Industrial Estate (see map). This offered the advantage
of being able to deliver coal by either canal barge (the adjacent
canal lock, no. 51, still boasts a sign “Gas 1”) or by railway
wagon. However, as it was presumably impractical to off-load coal
directly at the gasworks, a dedicated feeder line (a horse-drawn
tramway) was built
at the end of the railway goods yard, to the west of today’s station
car park. As this lay to the north of the main railway line (at that
stage The London Midland and Scottish Railway), the tramway utilised
an existing pedestrian subway tunnel to reach the gasworks on the
south side, a total distance of approximately 400 yards. The tunnel
still exists today but is sealed with a metal gate.
Coal was unloaded from the main railway wagons into a small bunker
and thence into the skips on the tramway, which had a gauge of 18½ inches. According to
Contact magazine (date unknown, but probably early 1950s),
the German engineering firm Krupps of Essen
made the tramway rails. The skips apparently held about six
hundredweight of coal (approximately 305 kilos) and in the earlier
years, a load consisted of four skips.
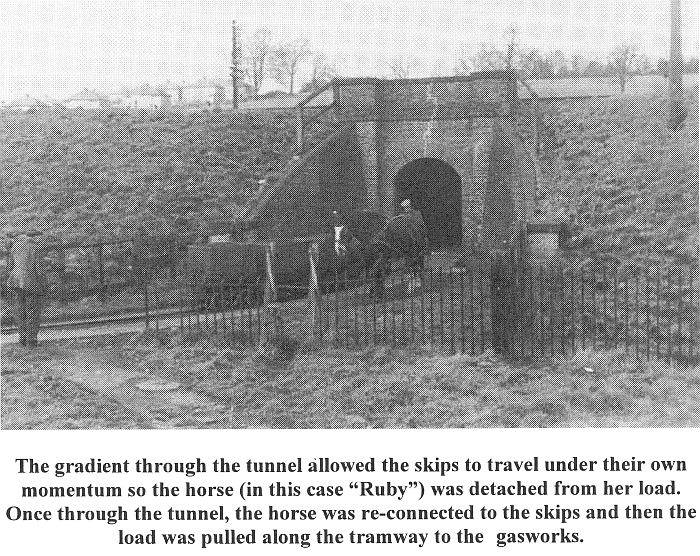
A letter written to H. C. Casserley by the Eastern Gas Board in 1955
confirmed “Horse traction has always been employed. ‘Kitty’
a fine
mare, did the job for many years, then came Billy and following him
our present mare ‘Ruby’. While in 1906 ‘Kitty’ handled a maximum
coal requirement of 10 tons, ‘Ruby’ now deals with a maximum of 50
tons”. Apparently this was a daily figure and Ruby was
able to pull five
skips, thus about 1½ tons per journey. H. C. Casserley’s article in
the Railway Bylines magazine of April 2005 stated that by “the 1930s
more than 5000 tons of coal was conveyed by the tramway each year”.
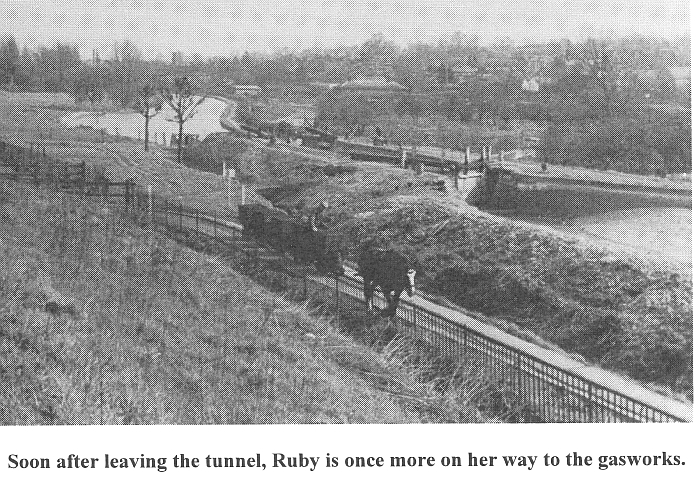
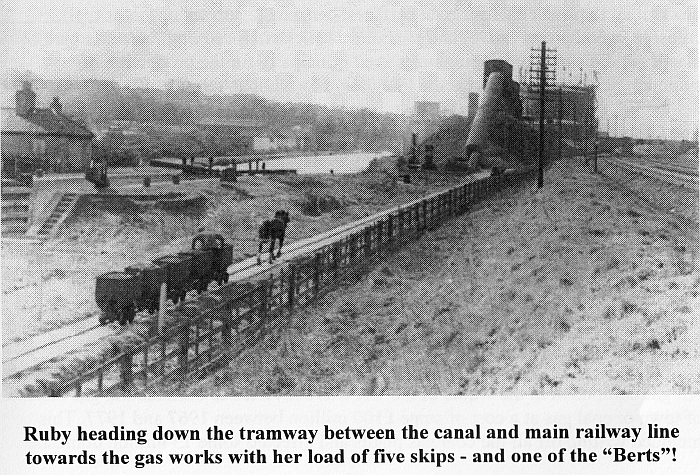
The Contact magazine article also identifies the two staff operating
the tramway at that time who were nicknamed “Old Bert” and “Young
Bert”. Old Bert in reality was Herbert Alfred Hartup, originally a
cowhand who became a stoker. Married with five children, his name
persisted in one son following his footsteps by helping out at the
Watford gasworks. Young Bert was Bertram Hannel and was not related
to Old Bert.
Ultimately “horse traction” was overtaken by mechanised transport.
The gasworks ceased production in 1955 and was finally closed in
August 1959. The two gasholders (or gasometers) continued to be used
for storage for some years and the tramway tracks were mostly
removed in the 1970s; a short section still lies in the subway
tunnel.
So, what happened next? To start with, coal gas continued to
be supplied to Berkhamsted but from the gasworks at Boxmoor where
the gasholders still persist. The composition of gas varies
according to the type of coal used and the temperature at which the
heating process or carbonisation takes place. A typical
breakdown might be: Hydrogen 50%, Methane 35%, Carbon Monoxide 10%
and Ethylene 5%; only the latter produces a luminous flame but as explained above, this can
be greatly enhanced with the use of a mantle. Depending on the
quality of coal used, the process of making gas generated
by-products such as coke, coal tar, ammonia and sulphur all of which
had their own end-uses. Coke provides a smokeless fuel but can also
be used to generate other types of gas and in metallurgical
manufacturing where a higher temperature is required. Coal tar can
be distilled to produce tar for road surfaces, benzene (a solvent or
motor fuel), creosote (wood preservative) and phenol/carbolic acid
(used in the manufacture of plastics and disinfectants); sulphur is
used principally for the production of sulphuric acid and ammonia is
the foundation for various fertilisers.
The Gas and Coal Act of 1948 created a nationalised industry
throughout the UK and in the 1960s, natural gas was discovered under
the bed of the North Sea and a new national distribution network of
some 3000 miles was established. Apart from being a readily
available supply of indigenous energy, natural gas has the
advantages of being non-toxic and requires little processing. Town
gas contained
extremely poisonous carbon monoxide and both accidental poisoning
and suicide by gas were commonplace. Poisoning from natural gas is
possible if incomplete combustion occurs and carbon dioxide
accidentally leaks into living accommodation. Both town and natural
gas are odourless and thus a foul-smelling substance (mercaptan) is
added to allow detection if gas leaks occur.
All gas equipment in the whole of the UK was converted to burn
natural gas instead of town or coal gas at a cost of some £100
million between 1967 and 1977. This included writing off all the
coal gas plants and affected some 13 million domestic customers,
400, 000 commercial users and 60,000 industrial customers. The town
gas industry died in 1987 when the last plant was closed in Northern
Ireland. It is interesting to speculate that with natural gas now
being a world commodity and subject to the vagaries of international
trade, supplies may be subject to disruption or even disconnection. The possibility of supplies also being depleted might suggest the
possibility of a return to the manufacture of coal gas in the future
especially where substantial reserves of coal remain available.
――――♦――――
References:
The minutes and accounts for The Great Berkhamsted Gas Light and
Coke company 1849 to 1905 — held for the Berkhamsted Local History
and Museum Society in the Dacorum Heritage Museum Store
Wikipedia
Encyclopaedia Britannica - DVD2000
A Short History of Berkhamsted — P. C. Birtchnell
Contact magazine
Railway Bylines magazine (April 2005) H. C. Casserley
Photographs — R. M. Casserley and H. C. Casserley
Britishgasacademy.co.uk
The London Encyclopaedia — edited by Ben Weinreb and Christopher
Hibbert (1983 revised 1992)
――――♦――――
First published by the Berkhamsted Local History and Museum
Society in
The Chronicle Vol.VI. March 2009
――――♦―――― |