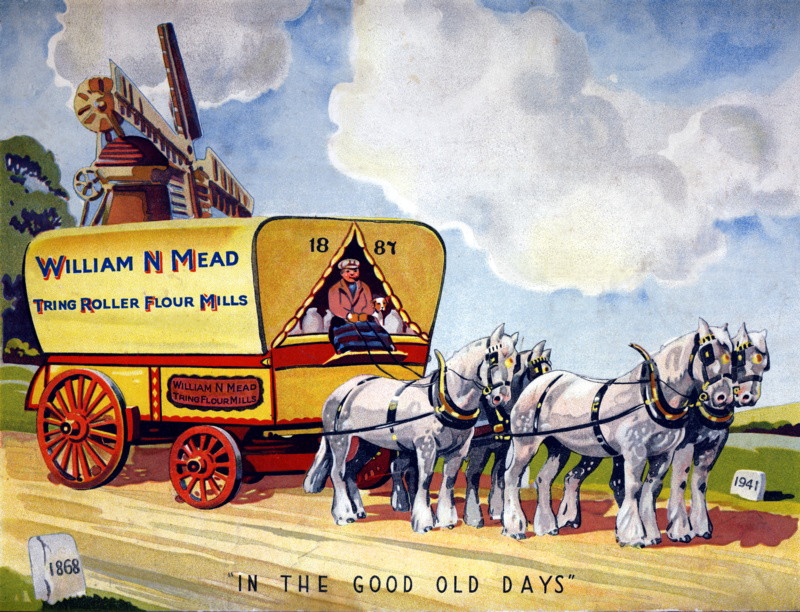
FOREWORD
In Tring, malting barley, straw plaiting, silk throwing, canvas
weaving, iron-working, vehicle body building, coaching inns, the
construction of canal craft (at Gamnel) and of lock gates (at Bulbourne) and the
manufacture of coal gas (The
Tring Gas Light & Cole Company) are some of the businesses that over the
years have come, and have gone.
Tring recently reacquired a brewery to replace the
several – if pub brewing be included – that once existed in the
town, while the sewage works at Gamnel can trace its roots back at
least 140 years. [1] This leaves just one important
and long-established business, grain milling. Milling has taken place at Gamnel for over two centuries,
longer if an earlier watermill that is known to have existed in that
locality is included. The following account is,
therefore, the story of Tring’s oldest continuous business, the
manufacture of flour.
ACKNOWLEDGMENTS
My thanks go to Mrs Heather Pratt, grand-daughter of William Mead
of Tring Flour Mill, and to Miss Catherine Bushell, whose father and
uncle were proprietors of the Tring Dockyard, for allowing me to use their
family photographs and papers. I am also grateful to Paul
Messenger, Manager of Heygates’
Flour Mill, for an interesting and informative tour of the mill and
its packaging plant (also for
some free samples of the product) and to Wendy Austin for her help
with research and editing.
Ian Petticrew
April 2017
――――♦――――
CONTENTS
THE NEW CANAL AND
GAMNEL WHARF
THE GROVER FAMILY
THE MEAD FAMILY
STEAM-POWERED MILLING
WIND MILLING GIVES WAY TO
ROLLER MILLING
THE MILL UNDER WARTIME
CONDITIONS
HEYGATES ACQUIRES THE
BUSINESS
TRANSPORT
THE BUSHELL BROTHERS’
BOATYARD
TRING FLOUR MILL TODAY
――――♦――――
THE NEW CANAL AND GAMNEL WHARF
An early product of the Industrial Revolution was our canal network, which improved
quite dramatically the
means of transporting goods, particularly those in bulk such as coal,
grain and manure (for in that horse-powered age, large quantities were shipped
from the cities to fertilise the land). Many local businessmen and farmers soon became aware of the
potential benefit that canal transport would have on
their profits, and factories, mills and wharfs soon sprang up along the banks of the new waterways.
The Grand Junction Canal (since 1929, the Grand Union Canal) reached
north-west Hertfordshire at the end of the 18th century.
Fortunately for Tring, which would otherwise have been bypassed, the need to provide the
Canal with a
reliable
water supply as it crossed the ridge of the Chilterns led to
a plan to construct a feeder ‘ditch’, which led westwards along the
contour between Bulbourne and Wendover, passing the northern
outskirts of Tring on its journey. However, pressure from local farmers and land owners
led the Grand Junction Canal Company (GJCC) to apply to
Parliament for an Act to make the ditch navigable.
In due course the following
statutory notice appeared in the newspapers published along the
route
of the GJCC, giving notice of the Company’s intention to apply to
Parliament for an Act which, among other things, would authorise
them:
“. . . . to make navigable, the cut or
feeder now making, and intended to be made, by the company of
Proprietors of the Grand Junction Canal, from the town of WENDOVER,
in the said county of Buckinghamshire, to the summit-level of the
Grand Junction Canal, at Bulbourne, in the parish of Tring, which is
to pass in, to, or through the several parishes of Wendover, Halton,
Weston-Turville, Aston-Clinton, Buckland, and Drayton-Beauchamp, in
the said county of Buckingham; and the parish of Tring; till it
joins the said summit-level at Bulbourne aforesaid. Dated this 5th
day of September, 1793.”
E. O. Gray, Aston
Chaplin, Clerks to the Company.
Exactly when the Wendover Arm was completed is unknown, but it was
probably shortly after 1794, for in his progress report of May of that year
Chief Engineer William Jessop states that “About seven-eights of
the Wendover Canal is cut”, and in a GJCC circular of November,
1797, reference is made to “The Wendover collateral line, now
finished for the sake of the water.” Thus, the Arm was widened and made navigable, and
wharfs were built at, among other places, Gamnel (Tring), Buckland and Wendover to
cater for the trade that commenced when the main line of the canal reached Bulbourne
Junction in
1799.
The earliest reference to milling in the
Gamnel locality is also in that year. The site now occupied by Tring Flour Mill (Heygates Ltd.) was in the vicinity of a water mill –
probably located near the Baptist Chapel in New Road – that had been bought
by the GJCC and then dismantled, its water supply having been
diverted into the canal summit. The loss of the mill pond affected the local Baptist community, whose
traditional baptism ceremonies were thus curtailed:
“The Water Mill at New Mill is now sold to the Canal Company, and the pond
cannot therefore be used in future for baptism. A baptistery is
being made in front of the pulpit in the Chapel [where it
remains].
The Mill had previously been in the ownership of friends of the
Chapel, and after a baptismal service the women used to change their
clothes there, and the men walked up to the Chapel to change. The
open-air baptisms were a good thing [to be] done away with, although
they were greatly preferred by the Minister and some members of the
Chapel. The services were always scenes of much hostility and abuse
from certain people in Tring, the participants in the service
oftentimes being pelted with filthy missiles.”
From the Tring
Vestry Minutes for
1799.
Then, on the 14th October 1800, the GJCC Minutes record that a wharf at Tring
– presumably
that at Gamnel, now generally known as
“Tring Wharf”
– was sold by auction for three years from 29th September. It
was taken by James Tate, a coal merchant and barge owner, for £15
per annum. The first reference to
“Gamnel”
appears in a deed of transfer held by Dacorum Heritage Trust dated the 5th July 1810, when
the GJCC sold the freehold of what appears to have
been the
same site . . . .
“. . . . by Deed Poll under Common Seal in Consideration of Four hundred
pounds paid to them by the said William Grover grant and release to
the said William Grover his Heirs and Assigns All that wharf Land
and Buildings thereon containing one acre and three roods more or
less situate next Gamnel [canal] Bridge in the Parish of Tring . . . . ”
. . . . which, with some later extensions, is the site now occupied
by Heygates flour mill (see map below).
|
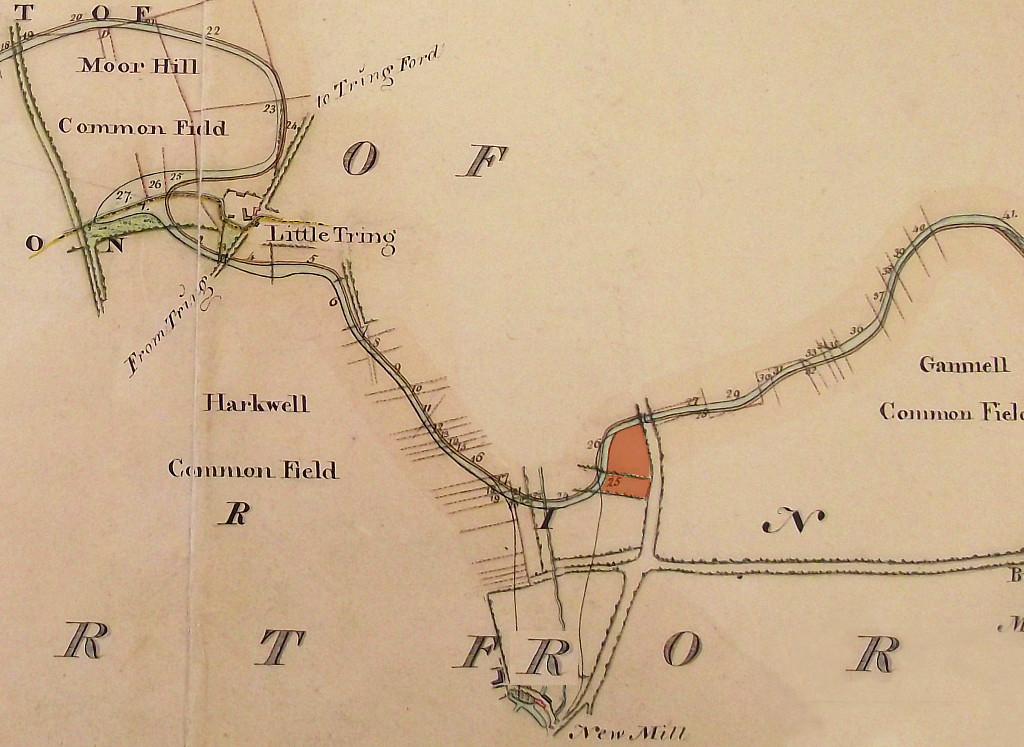
A section of the GJCC's plan
for the Wendover Arm, the numbers identifying the respective land
owners.
The canal company bought the Gamnel site –
plots 25 & 26 (shaded red), comprising an area of 1 acre and 3 roods
–
from Henry Harrison and William Butcher respectively.
――――♦――――
THE GROVER FAMILY
William Grover must have seen a business opportunity in further
developing the Gamnel site on which “wharf
Land and Buildings”
did already exist.
On it he (or perhaps his brother James) later erected a windmill and
set up in business sending and receiving goods by canal. Exactly when the windmill was built is unknown. Andrew
Bryant’s 1820-21 map of Hertfordshire includes a windmill symbol at Gamnel Wharf,
while Pigot’s Directory for 1823 lists the brothers William and
James Grover as ‘millers’ at Gamnel, but the earliest record of
Gamnel
Wharf and premises is in 1829, when they were held by William
Grover, while James Grover held the windmill and a house on the same
site, at a rateable value of £13. 5s. 0d.
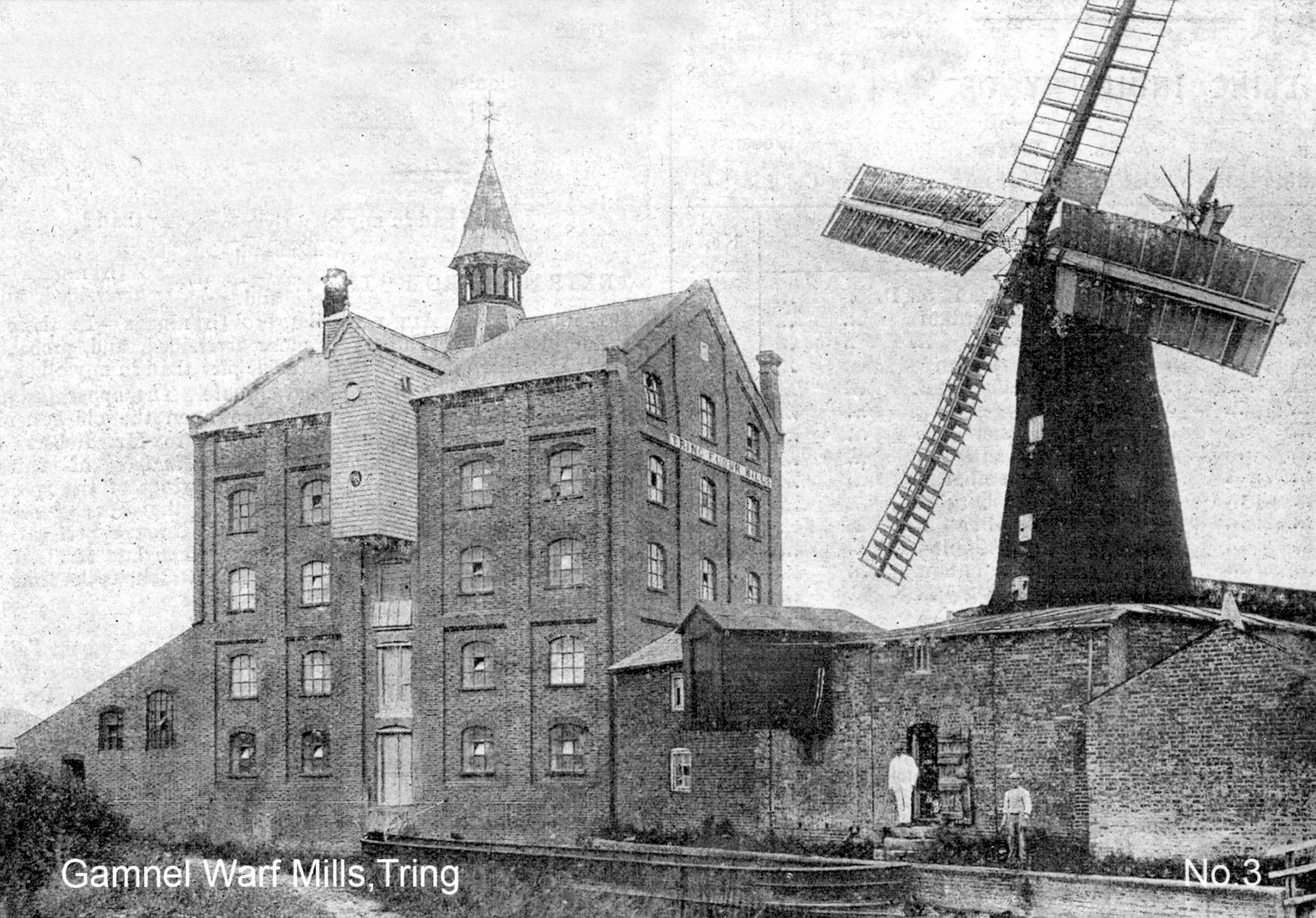
Viewed from across the Wendover
Arm, the steam mill erected in 1875
and the tower mill demolished in
1911.
Old photographs show the mill to have been a brick-built 6-storey
tower mill with a gallery on the second floor. In its latter
days its four sails were of the double-shuttered patent type.
The cap was in the ‘Kentish style’, winded by a fantail with an
extension at the rear to support the fantail’s stage. It was
considered to be a relatively large mill having power sufficient to
drive at least three pairs of millstones. While no record
exists of the mill’s machinery, it was probably comparable to that
in the later tower mill at Quainton and, judging from photographs of Gamnel Mill, was of similar
external size and appearance.
At some time after 1829, the partnership between the Grover brothers
ceased. Why is unclear, but following their father’s death in
1820 there arose a prolonged dispute between them concerning the terms of his will. In her
history of Aldbury, Jean Davis refers to a vestry dispute of 1828,
and states that . . . .
“The fact was that, at some time before he died in 1820, John Grover
had given up his baker’s shop in Aldbury and moved to Tring Wharf. Having acquired some land in North Field, he proceeded to build a
house there adjacent to the road, which he left to his son James
with the crop and implements and household goods. According to John
Clement, watchmaker and Baptist preacher of Tring, James’s brother
William disputed the will, which finally went to arbitration. James
is reported to have said that he was wronged of ‘hundreds of
pounds’.”
For whatever reason, James Grover set out to build and work the nearby
Goldfield windmill in competition with his
brother, which is where the 1839 edition of Pigot’s Directory
lists him. The mill at Gamnel Wharf continued to be run by William in partnership with his son Thomas, while the pai ralso
ran a canal carrying business, their listing in Pigot’s trade
directory for 1839 advertising services “To
London and all places on the line of the Grand Junction Canal, and
goods forwarded to all other parts of the Kingdom, by Grover and
Son, from Gamnel wharf, and Thomas Landon, from Cow Roast wharf,
daily.”
The 1841 Census records William
Grover, then age 60, at Gamnel with his son Thomas, and the Hillsdons, father and son, who were later to set up business as
millwrights in Chapel Street, Tring, all four being
described as millers. But the business was not to last much longer.
In January,
1843, a brief notice in the London Gazette announced the
dissolution of the partnership between William Grover & Son, wharfingers, of Tring Wharf and Paddington.
In the following month, a notice appeared in the
Bucks Advertiser announcing that:
“William Grover, in the town of Tring in the County of
Hertfordshire, having on the 28th day of January last disposed of
the business of wharfinger, coal and coke merchant and mealman, and
dealer in hay, straw, ashes, and other things, lately carried on by
him in partnership with Thomas Grover, at Tring Wharf, and at
Paddington in the County of Middlesex, under the firm of ‘WILLIAM
GROVER & SON’ to his sons-in-law, William Mead and Richard Bailey.
Messrs. Mead and Bailey beg to announce that they will continue to
carry on the same business, upon the said premises, in partnership
under the name of ‘MEAD & BAILEY’. All debts due to and owing from
the said William Grover, will be received and paid by Mead &
Bailey.”
The inherited rumour is that William Grover became insolvent, but a
book held in the Herts Records Office based on correspondence
between the deacons of New Mill Baptist Chapel and William Grover
attribute the reason to illness:
“He [William Grover]
had a sad end. He became ill and descried to make the business
over to Richard Bailey and William Mead – they took over the Wharf
and it was conveyed to them, and paid annuities of £100 to Wm. and
£90 to his son during their lives -
‘since
it has been said that his circumstances being in a deranged state,
caused his illness, if he was ill, which some thought not the case.’
Thus the Wharf and house that he had erected passed away from
himself, his son and grandson, and his name perished from his
inheritances after the sudden death of Richard Bailey in Feb. 1856.”
Characters against Clements 1853 (ref:
D/EHn Z48/6, Herts Records Office)
It is interesting that the Grovers described themselves not as
millers, but as “wharfingers”, which suggests that their
principal business activities were the shipment of produce by canal
and the resale of imported bulk commodities, such as coal, coke and
manure.
In an age before the development of road transport and with the
nearest railway goods yard almost two miles from Tring town centre,
the Wendover Arm was not only an important source of water for the
Grand Junction Canal, but of commercial importance to the town and
its surrounding area. Indeed, it is known that the Arm was
used to convey grain not only to the windmill at Gamnel, but also to that
at Wendover, it too being located
strategically close to that town’s canal wharf.
After 1843 the Grovers disappear from the story of the mill, and for
the following century Tring Flour Mills were owned, either in
partnership or in the sole possession of members of the Mead
family, eventually becoming known as Mead’s
Flour Mills.
――――♦――――
THE MEAD FAMILY
Following the change of ownership, Messrs. Mead and Bailey continued to offer a diverse range of
services at Gamnel Wharf, advertising themselves as millers, coal merchants, wharfingers
and water carriers. They were also dealers in horse manure, which they
imported by canal from London sending cargoes of hay and straw in
return. It is likely that Bailey managed the wharf, for in the 1851 Census he describes him as “Miller
and Wharfinger” while Mead appears as “Farmer and Miller”(the Mead
family continue to farm in the area today). Their workforce numbered around 30 men, which the Census
lists living (with their families) in the
immediate vicinity of the mill, which covered only half the area of
that taken up by the mill today. William Mead lived on
site in a handsome house adjacent to the yard. However, it is open to question
whether this was a close-knit and caring community, for a
contemporary account relating to one of the mill’s employees rather
belies this view.
William Massey, who worked as a labourer at the mill, lived with his
family on the wharf where he rented a hovel from the miller for a
shilling a week. David Shaw, in his
biography of Gerald Massey,
William’s eldest son, writes:
“For this money they [the Massey
family] were given a damp flint stone hut
with a roof so low that it was impossible for an average adult to
stand upright. Having paid the rent, nine shillings remained from
William’s weekly wage to provide a minimum subsistence.”
In his autobiographical sketch, John Mead, William Mead’s sixth and
youngest son, also refers to the cottages (and to the
windmill):
“We are sometimes told that adults do not generally remember
anything that happened before they were 5 years old, unless of a
very special character. Such a special happening did take
place in my case, for the neck of a windmill broke, and the sails
all tumbled down together. This is my earliest recollection, and I
was then but 3 years old [i.e. 1849].
It was the custom in those days for mothers to send their children
while very young to such schools as were convenient, so that they
could get on with their work without being hindered by the presence
of the little folks, and I was sent, with my cousins the Baileys,
when under 4 years old. My first school was at Mam Rowe’s, who lived
in one of 4 houses in a row of 4 flint cottages. The next one was
occupied by Mr. and Mrs. Massey, parents of the better known Gerald
Massey, the poet; and the others by Thomas Rowe, a stoker at the
mill, and Joseph Anderson. The rent of these cottages, including
good gardens, was about 1/- per week. At Mam Rowe’s school we sat in
a row on a form about 1 foot high, and there I learned the
alphabet.”
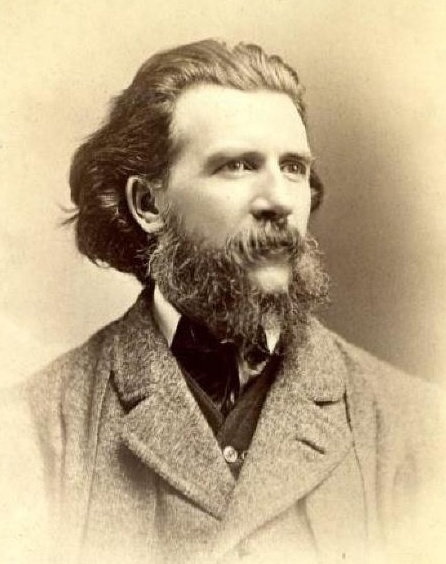
Gerald Massey (1828-1907),
poet, critic and writer
on Ancient Egyptian beliefs.
Gerald Massey was to become a Chartist agitator, later acquiring
renown in literary circles as a poet, critic and author. Some years after
William’s death, Gerald Massey had this to say about his late
father’s employment at Gamnel Wharf . . . .
“I know a poor old man who, for 40 years, worked for one firm and
its three generations of proprietors. He began at a wage of 16s. per
week, and worked his way, as he grew older and older, and many
necessaries of life grew dearer and dearer, down to six shillings a
week, and still he kept working, and would not give up. At six
shillings a week he broke a limb, and left work at last, being
pensioned off by the firm with a four-penny piece! I know whereof I
speak, for that man was my father.”
Regardless of whether the Meads treated their employees in such a
Dickensian manner, their business prospered. However, the partnership between Mead & Bailey
was to end in 1856
with Bailey’s death.
In the following year his widow Sarah bound their
son Thomas as an apprentice miller to Edward Mead for a period of
five years.
The details of whatever financial settlement William Mead reached
with Sarah Bailey do not survive, but following her husband’s death
sole ownership of the mill
passed into the Mead family, beginning with William.
By the 1860s ownership of the mill had passed jointly to William’s
sons, Edward and Thomas, but in 1865 Edward sold his share to
his brother John, who three years later sold out to Thomas, leaving
Thomas Mead the sole owner of the business. In the same year
Thomas extended the site with the purchase of an adjoining plot of
land facing the Wingrave Road (curiously, the purchase document
describes his occupation as “farmer”).
Although not relevant to the milling business, it is interesting to
see the nature of the canal trade that was still being carried out
at Gamnel Wharf despite the damaging impact of the railway.
This from John Mead’s autobiographical sketch . . . .
“My next move was to Gamnel Wharf, where I was born – my brother
Albert who had the hay and straw trade there was a bachelor.
He had done well in business, and offered to let me have it which I
did, taking it over in 1879, when I was 33 years old. I then
became coal merchant, lime burner, and dealer in artificial manure
etc., sent hay and straw to Paddington by canal, and had stable
manure for the return journey . . . . I had nothing to do with the
sale of hay and straw at 5 South Wharf, Paddington. My brother
Albert arranged with another brother, Frederick, to pay commission
of 1s. on each load of 36 trusses of straw, and 5s. on each ton of
hay, and he charged 2s. 6d. for each ton of manure brought back by
boat.”
. . . . from which it is fair to conclude that at this date the
Wendover Arm remained important to local farming interests.
Thomas Mead was blessed with five sons (of which Thomas Mead Jnr. died in
his youth) and two daughters. In the late 1890s Thomas Mead Snr. bought Clifford Mills, Northampton, and this business was
managed by Frank and Duncan Mead, until Duncan was killed in the
Boer War; Frank then carried on the business alone for many
years. Of the other two sons, Percy later took over Gubblecote
Farm, Tring, which his descendents continue to farm, and, in 1898, William
bought the Tring Flour Mill from his father in exchange for an annuity
of £200 p.a.
William Mead then carried on the business
successfully until his death in 1941, at some time also farming
Old Manor Farm, Wingrave; Hospital Farm, Marsworth; and Silk Mill
Farm, Tring. And until government restrictions caused it to be
discontinued following the outbreak
of World War II., he also ran a
successful retail coal business from the wharf.
――――♦――――
STEAM-POWERED MILLING
By the 1840s it appears that a steam engine had been installed to supplement wind power,
which by then was fairly common practice, for in his
autobiographical sketch John Mead refers to one of the occupants of
the mill cottages as
“Thomas Rowe, a stoker at the
mill”
(the 1861 Census lists
19-year old Samuel Bull as an “engine stoker”). Nothing is known about the steam
engine, but later evidence suggests it was separate from
the windmill, unlike the practice adopted at Wendover where a
small steam engine was installed beside the windmill and coupled to
its spur wheel (which drove the millstones, etc) via an iron shaft
and cog.

Wendover windmill and engine
house.
The
flue from the engine’s boiler passed underground to a tall
brick-built chimney in the centre of the mill yard.
By this date the business at Gamnel Wharf was run by William Mead’s
sons Thomas and Edward (who also rented Wendover windmill).
Edward had become a busy man, having acquired milling interests at
Watford, Hunton Bridge and Chelsea.
But having sold his share of the business to his younger brother
John in 1865 (see previous section), Edward Mead departs from the
story of Tring flour mill. John Mead then carried on in
partnership with Thomas for 3 years, as he records in his
autobiographical sketch . . . .
“Prior to my return home Gamnel [a.k.a. Tring]
Flour Mill was run by my brothers Edward and Thomas, but the former
took the mill at Hunton Bridge, near Watford, and said I might have
his share of Gamnel for £1500. This I accepted, giving notes
of hand [i.e. promissory notes],
which I paid off when I had earned the money. I worked hard,
sometimes up to 10 o’clock, and if windmill and steam-mill
were both working I would stay until 1.00 o’clock in the
morning.
In these cases I slept at my brother William’s house . . . .
After being a miller for 3 years, my brother Thomas took the
business, and I became a farmer. This was in 1868 when I was
22 years old, but farming was not so remunerative as milling.
I should have made more money at the mill.”
. . . . after which John also leaves the story of the Tring Flour
Mill.
A particular
milestone was reached on the 1st March, 1875, when Thomas Mead took the bold step
of signing a contract for the construction of an imposing brick-built grain mill adjacent to the
windmill. The builder was one Duncan Stewart of Wallington, in
Surrey, who undertook to build the mill for the sum of £1,246, the contract
stipulating that the building was to be complete by the end of July
against a penalty of £2 for every week over-run.
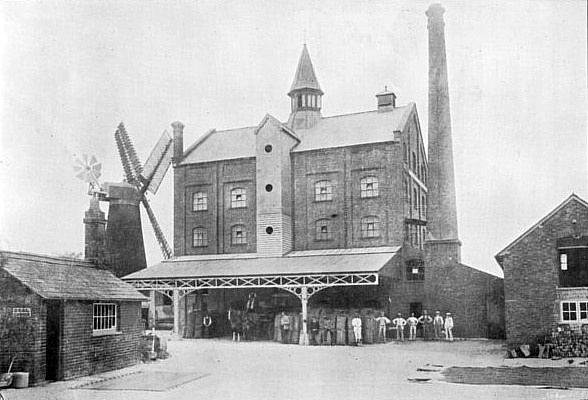
The new steam mill. It
consisted of five spacious and lofty floors
fitted with the
necessary storage bins.
The new mill was powered by a beam engine capable of driving five pairs of
millstones.
Installation of this new machinery did not go without incident,
as one local newspaper reports . . . .
“Accident — There was a shifting of the old boiler out of the old
engine house at Mr Thomas Mead’s flour mill into the new one on
Tuesday; and in order to do this, the boiler had to be raised four
feet. A small space had been left at the end for the jack, and the
block underneath slipped when the boiler was raised about two feet,
and caused the boiler to run ahead, striking against Lot Denchfield,
fracturing his right thigh and left fore arm. Denchfield was at once
taken to the County Infirmary at Aylesbury.”
――――♦――――
WIND MILLING GIVES WAY TO ROLLER MILLING
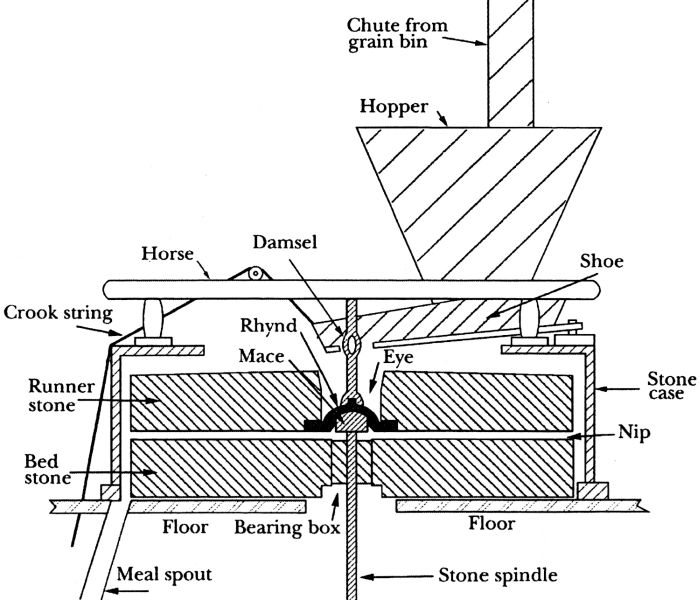 |
Schematic
illustration of traditional
milling equipment. |
The
age-old process of producing flour was to crush wheat between
two circular millstones. Of the two, the lower ‘bed stone’
remained stationary while above it the ‘runner stone’, which
does the grinding, was caused to rotate under the power of a
windmill’s sails or a waterwheel (a few combined wind and
water mill also existed, Doolittle mill at Totternhoe been a
nearby example). Under gravity, wheat trickled into the
eye of the rotating runner stone from where it was channelled
between the faces of the two stones. The rotating runner
stone then subjected the wheat to a ‘scissoring’ or grinding
action that produced ‘meal’. The runner stone was
generally slightly concave, while the bed stone was slightly
convex. Under the rotating action of the runner stone,
this shaping channelled the meal to the outer edges of the
stones where it was gathered up.
A ‘flour dresser’ was then used to sift the meal into various
grades of fineness. This consisted of a cylindrical drum
covered in wire mesh of increasing grades of fineness, and set
at an angle. Inside the drum revolved a set of brushes.
Meal, fed into the upper end of the cylinder was rubbed against
the mesh screens by the brushes as it fell through the cylinder
under gravity. The finest meal, white flour, passed
through the finest mesh screen; next came semolina flour, which
passed through the next grade of mesh, leaving the coarsest
product, bran. Each grade was ejected into canvas chutes
which feed sacks on the meal floor below.
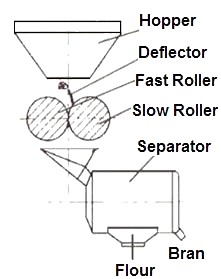 |
The principle of
the roller mill. |
As the 19th century progressed, advances in technology swept away
old industrial systems and grain milling was not exempt from
progress. Thus, in 1894 Thomas Mead took a further step forward
when he installed the recently-developed roller milling system,
running it for some years in conjunction with the windmill (which
was
probably relegated to grinding animal feed).
Roller milling made possible the construction of larger, more
efficient grain mills, hastening the abandonment of the small
country wind and water mills that used millstones to crush
the grain. The new system crushed the grain between a series
of fluted steel rollers of about 12 inches in diameter. The
rollers are set with a specified gap between them and spin towards
each other at high, but at different speeds; the surface of each
roller is also grooved with a different pattern. The input and
output to the milling equipment is through a system of pneumatic
pipes.
Roller mills
enabled the production of a larger amount of better-grade flour from
a given amount of wheat, quicker and to a much more consistent
standard than traditional stone grinding. (Appendix
1)
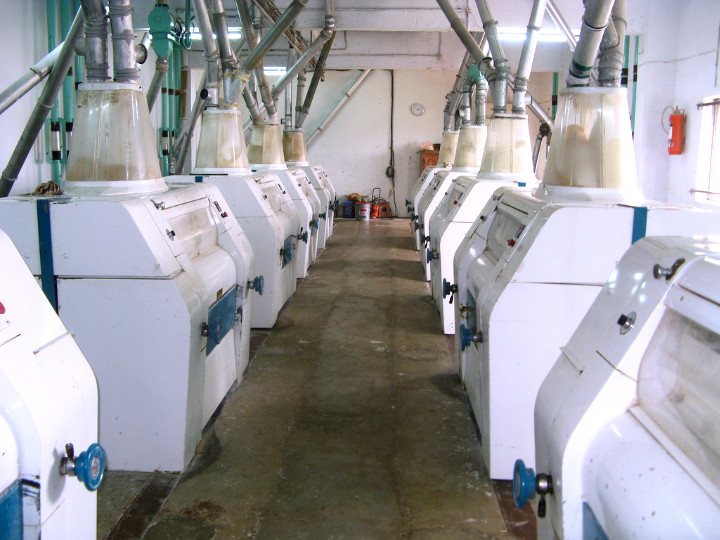
A modern roller flour mill.
Then, in 1905, Thomas’s son William, by then the mill’s owner, (Appendix
2) replaced the old Bolton & Watt-type beam engine with
a Woodhouse & Mitchell tandem compound condensing engine, rated at
120 hp, which drove the mill until it converted to mains electricity in
1946.
The early 20th century saw the rapid demise
of what windmills remained. After some ninety years of service Gamnel Wharf
tower mill was demolished on 4th May 1911. A local
newspaper gave the following account . . . .
“Removal of a Landmark — On May 4th a familiar landmark was
demolished. For many years the old windmill where Mr. Mead and his
ancestors have long carried on their business, has stood at Gamnel. The leisurely business methods of bygone days have had to give place
to more up-to-date arrangements and so the ground on which the old
mill stood was wanted for an extension of the steam-powered mills. Under the personal direction of Mr W. N. Mead the structure was first
undermined, wooden struts taking the place of the brickwork and when
it was ready a steel cable and winch hauled it over.”

The demolition of Gamnel Wharf
tower mill, 4th May 1911.
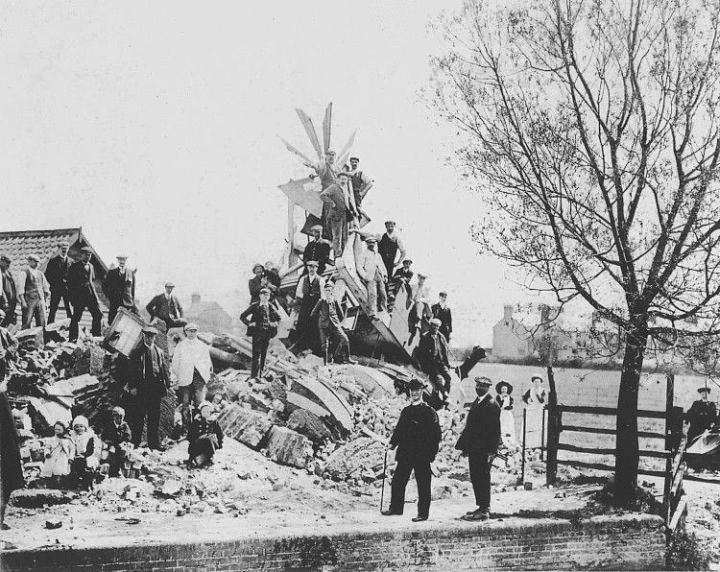
――――♦――――
|
THE
MILL UNDER WARTIME CONDITIONS
Following the demolition of the windmill, nothing is then on record
until the 1930s. This was a time of severe depression
throughout the land, which included farming and milling. Subsidised French flour was brought into this country
for as little as 12s 6d (twelve shillings and six pence) a sack of
280 lbs. Wheat was selling for about 18 shillings a quarter
(4½ cwts or 229 kilos), and even home-produced flour was as low as
17 shillings and 18 shillings a sack, but with the inception of the
Wheat Act (1932) [3] conditions gradually improved
and farming became more secure. Then, at the outbreak of World
War II., in common with all other flour mills, Tring was brought
under the control of the Ministry of Food. No-one envisaged at
the time that this control would last until August 1953, nearly 15
years! – indeed, government controls and restrictions on the
production and distribution of food grew even more severe for
several years following the return of peace.
During the war the
milling business was run under very difficult conditions. This
was due in part
to the rationing of a wide range of items, to manpower
shortage, and to stringent government controls implemented by the
Ministry of Food. In his autobiographical sketch,
Ralph Seymour, the mill’s
former General Manager,
describes working under Ministry of Food control:
“The
effect of the World War II on the mill was instant and shattering.
We came under the direct control of the Ministry of Food, who issued
an endless stream of Statutory Rules and Orders, which sometimes
contained twenty or thirty pages of closely printed instructions and
regulations, all couched in such legal jargon and phraseology as to
be almost incomprehensible. You needed the help of a lawyer to
decipher it all, so much so that one wag succinctly observed
‘You
don’t make a mistake today, you commit an offence!’
[4]
The mill
was now run on a constant 24 hours, 7 days a week basis. The
men worked 8 hour shifts − 6 a.m. to 2 p.m., 2 p.m. to 10 p.m., and
10 p.m. to 6 a.m. again, and these were worked on a rotation basis,
so that each man worked a different shift each week, on a 3-week
cycle. The only stops were made for essential repairs and
maintenance, but to get parts and machinery replacements you had to
sign applications ad nauseam to obtain a licence. Even
then you had to use every wile and trick known to man to actually
get the stuff! I have personally travelled 150 miles or so to
fetch a particular part.
Unfortunately
Harold Saunders, the flour traveller, died in 1940, and a few months
later Teddy Clarke also died. Replacement staff had to be
employed, and we were lucky to get an accountant, who came out of
retirement to help, and we also found a flour traveller who was
exempt from war service, but every firm then was having staffing
troubles, as so many were in the services, or munitions, or other
war jobs.
Soon,
all animal feeding stuffs were strictly rationed. Coupons were
issued to all owners of livestock, the number of coupons being
apportioned from returns made in previous years to a government
department, and depending on numbers and type of stock. Beef
farmers, for instance, fared very badly, as they were expected to
make full use of their grazing land, whilst producers of milk were
in a much better position.
The
coupons were valid for the month of issue and the subsequent month
only, and a strict account had to be kept of each transaction.
Officially, no customer was to become ‘overdrawn’ so to speak.
The coupons then had to be tabulated by us on special forms, fully
detailing the number and value of each coupon, and the quantity and
type of feeding stuffs supplied against it. Different forms
were required for the different types of feed-cereals, protein,
etc. The forms then had to be submitted to a central area
office, in our case Cambridge. On submission of the tabulated
forms to Cambridge, we were issued with Buying Permits, to enable us
to purchase more feeds for sale. At the end of each month,
these again had to be tabulated.
Under Ministry control the quality of flour was gradually lowered.
White flour became unobtainable, and the resultant output of
‘national’ flour produced a ‘standard’ loaf of a dingy grey crumb.”
――――♦――――
HEYGATES ACQUIRES THE BUSINESS
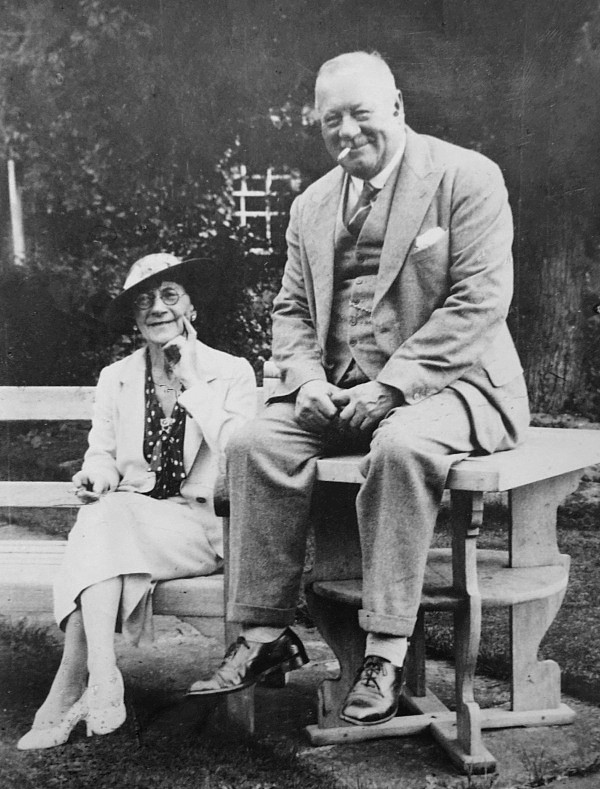
William Mead and his wife
Edith.
William Mead died in April, 1941. There being no son to
succeed him, the business passed into the control of his executors
and trustees. Ralph Seymour, who was a
minority shareholder in the business, [5] states
in his memoirs
that the three years following
William’s
death were a very unsettled period during which the
future of the mill was by no means clear. Then, early in July 1943,
Ralph
returned from a busy day on the London Corn Exchange to learn that
the mill had a new owner – he relates what then transpired:
“. . . . on coming into the office I
was introduced to a Mr. Robert Heygate. This gentleman said he
wished to consult me about the purchase of English grain from the
coming harvest. ‘In what connection, may I ask?’ I
enquired. ‘My family has bought the business of Wm. N. Mead
Ltd., and has paid a deposit,’ was the startling reply. ‘Well,
you haven’t bought me with it, have you?’ I responded. I
suggested that we should talk after I had dealt with all the affairs
of my London trip, and if he would accompany me to my home for tea
we could converse without interruption. Subsequent to my
meeting with Robert Heygate I agreed to travel down to their family
mill at Bugbrooke, Northampton, to meet his father and elder brother
Jack. I liked what I saw there. A family firm, they had
employees with upwards of 50 years in their service, which told its
own story.
I agreed to continue to manage the Tring business, but much of the
previous responsibility was off my shoulders. From the outset
the Heygates placed implicit trust in me and, as formerly, I
continued to be the sole signatory for cheques, etc. After
consultation, it was agreed that for the time being the Tring mill
would continue trading under the name of Wm. N. Mead Ltd; three
years later the trading title was revised to Meads Flour Mills Ltd.,
still with me in charge, and we continued under this name for a
number of years.
Despite the limitations of continued Ministry control and shortages
due to the war, I liked the Heygate approach, which was: ‘What
can we do to modernise,’ rather than the old Governor’s ‘Make
do and mend’ attitude.”
Messrs. Heygate and Sons, of Bugbrooke Mills, Northampton were – and
remain – a family business of millers, merchants and farmers.
The family, who had been farming the same land in Northamptonshire
since the 16th century, [6] moved into milling in the 19th
century, when Arthur Heygate Snr acquired Bugbrooke Mill. A
large change to the business came in 1942 when the mill was
destroyed by fire. It was rebuilt with state-of-the-art
milling equipment capable of converting 24 sacks of wheat into 18
sacks of flour every hour, plus bran for a feed mill alongside.
In 1944 the company acquired the Tring Flour Mill followed, in 1958,
by the Downham Market Mill. Subsequent investments have made
Heygates one of this country’s largest independent millers, while
the Group also has interests in a specialist milling business in
France.
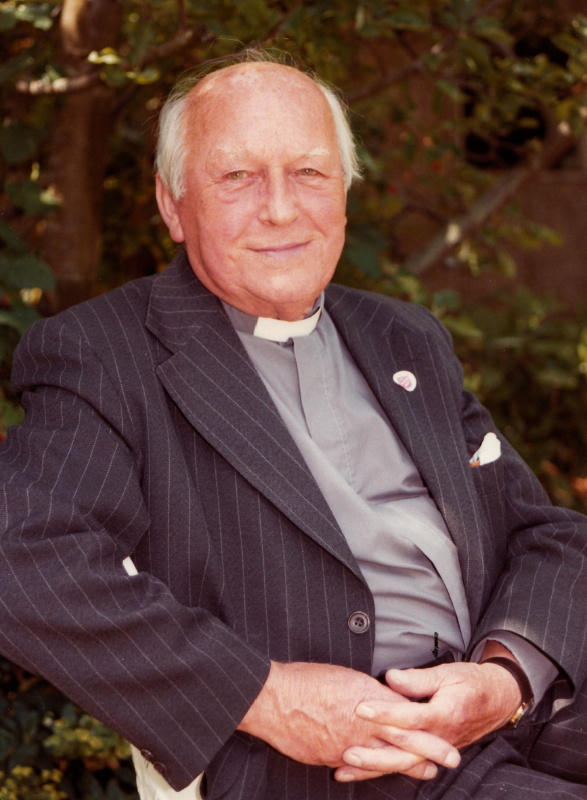
Ralph Seymour, for many years
General Manager of Tring Flour Mill.
Following
retirement Ralph was ordained and worked as a clergyman
in the Parish.
Following the takeover, the management of the Tring Flour Mill was
reconstituted. Ralph Seymour became General Manager and with
the return of peace the ravages of the war years were gradually
repaired. From 1946 to 1950 considerable extensions were made
to the warehouse and the offices. The conditioning bins were
increased in capacity and the intake of wheat by barge was
discontinued, with all supplies subsequently arriving by road.
This change created a very awkward bottleneck in the single road
access to the mill, the existing entrance being between the Mill
House building and the mill cottages. To remedy the problem
some 2 acres of land on the south side of the mill were purchased
from the Rothschild estate to permit a new access road to be laid
down. To make an entry, the old south boundary wall
was removed – this had formed part of the Carpenters’ Shop
and was the remaining part of the old windmill that had been pulled
down in 1911. Shortly after this work was complete it was
found necessary to extend the warehouse and the silo accommodation,
which until then were exactly as built nearly 40 years previously.
With the return to peace government wartime controls gradually
eased. Bread production was no longer limited to the national
loaf [7] and again became profitable. Good salesmanship in both
flour and feeding stuffs became essential. With the
mill remodelled, production increased and the business grew steadily.
Major re-arrangements of the flour milling procedures were again
undertaken in 1955-56 when the first pneumatic system was installed,
the third such installation in the U.K. Further major changes
took place during the 1970s, when additional bulk flour storage was
erected, and all the wheat cleaning plant and almost the whole of
the mill machinery was replaced. Careful management of this
project permitted the mill to continue to grind the same amount of
grain each week while the work was being carried out.
――――♦――――
TRANSPORT |
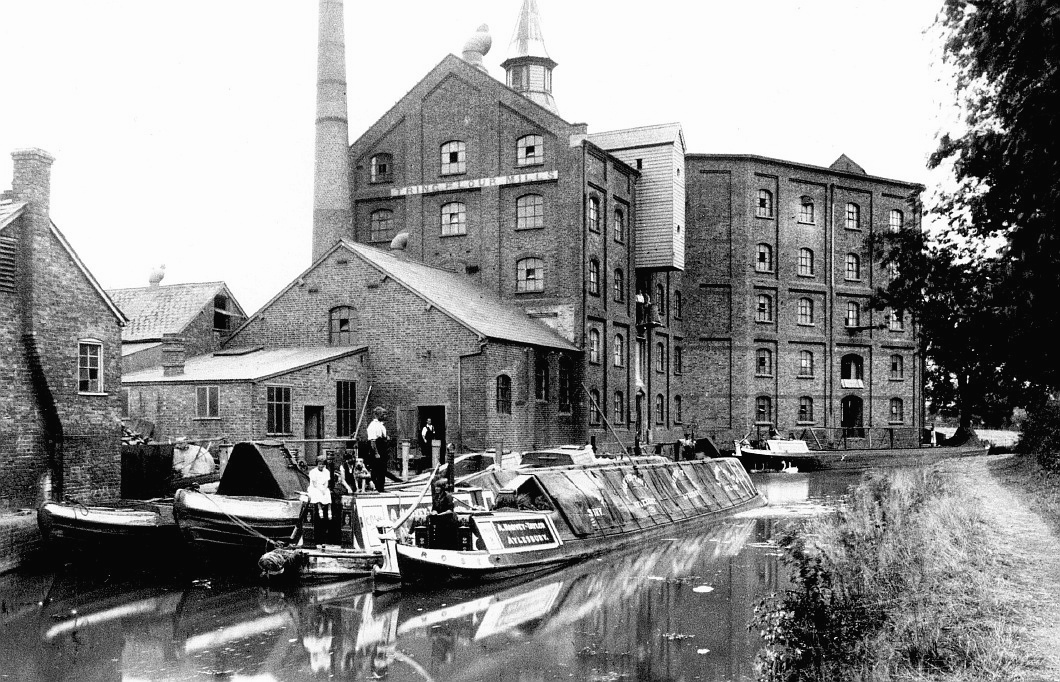
Above: A. Harvey-Taylor
(Aylesbury) narrowboats at Gamnel,
c.1930s.
Below: Mr. and
Mrs. Ward from Startops End with their daughter Phoebe and her
family.
They are discharging
Manitoba wheat at Tring Flour Mill.
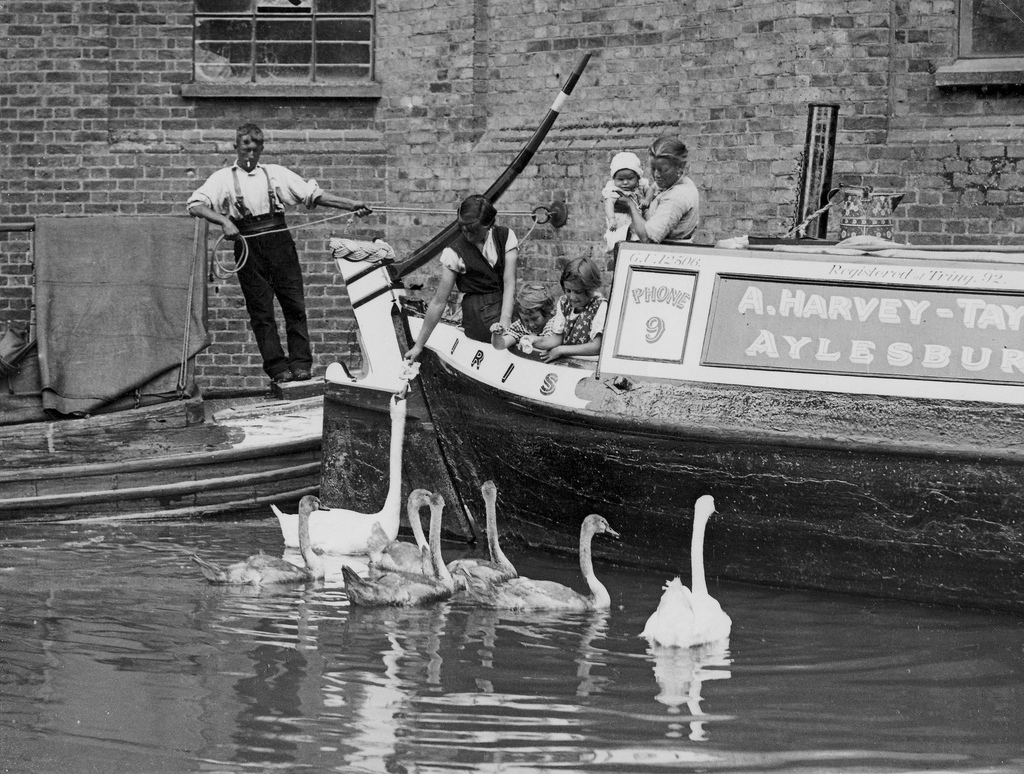
By the late 19th century much U.S. and Canadian imported wheat was
being exported to the U.K. In his
memoires Ralph Seymour says that it was shipped by barge from Brentford to Bulbourne, where it was transferred to a horse-drawn narrowboat for
its passage to the mill up the narrow Wendover Arm. However,
the above photographs suggest that wheat might also have been shipped
directly to the mill by narrowboat.
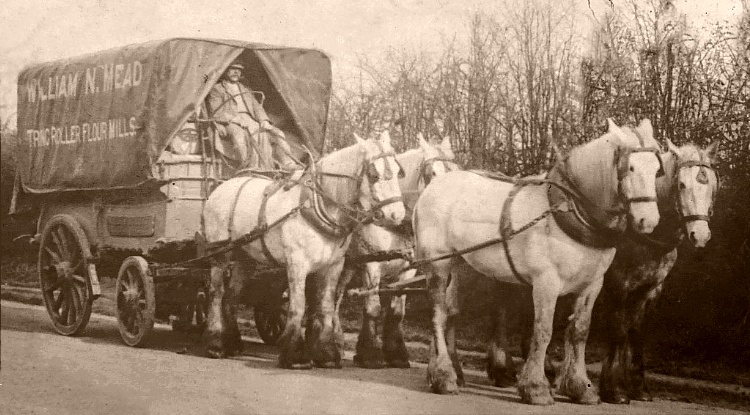
So far as local deliveries were concerned, before the Great War horse-drawn
wagons were used to deliver goods, with either 2-horse or
4-horse teams according to the load, the flour being delivered as far
as Chesham, Aylesbury, Leighton Buzzard and Dunstable. A
single horse van was used for smaller local deliveries. Then,
in 1916, a Foden steam wagon running on solid tyres and capable of
carrying 8-tons was first used; judging from the photograph below, a
Sentinel steamer also joined the fleet. In 1918, a 2½ ton
Napier lorry, also on solid tyres, was added, the body of which –
and of all succeeding lorries up until the Second World War – was
constructed by Bushell Bros. at their boatyard on the premises.
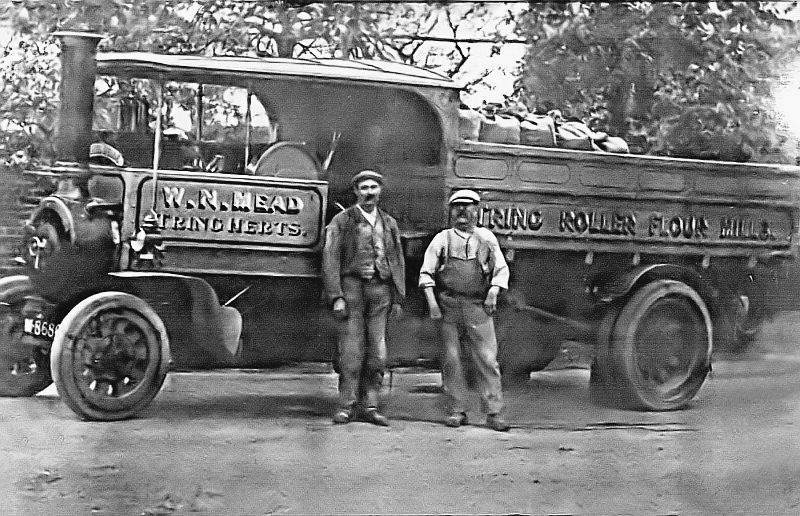
Above: a Foden steam lorry in
W. N. Mead livery. Below: a Sentinel steam lorry.

The intake of wheat by canal was discontinued soon after the end of
the World War II., with all supplies subsequently being delivered by
road.
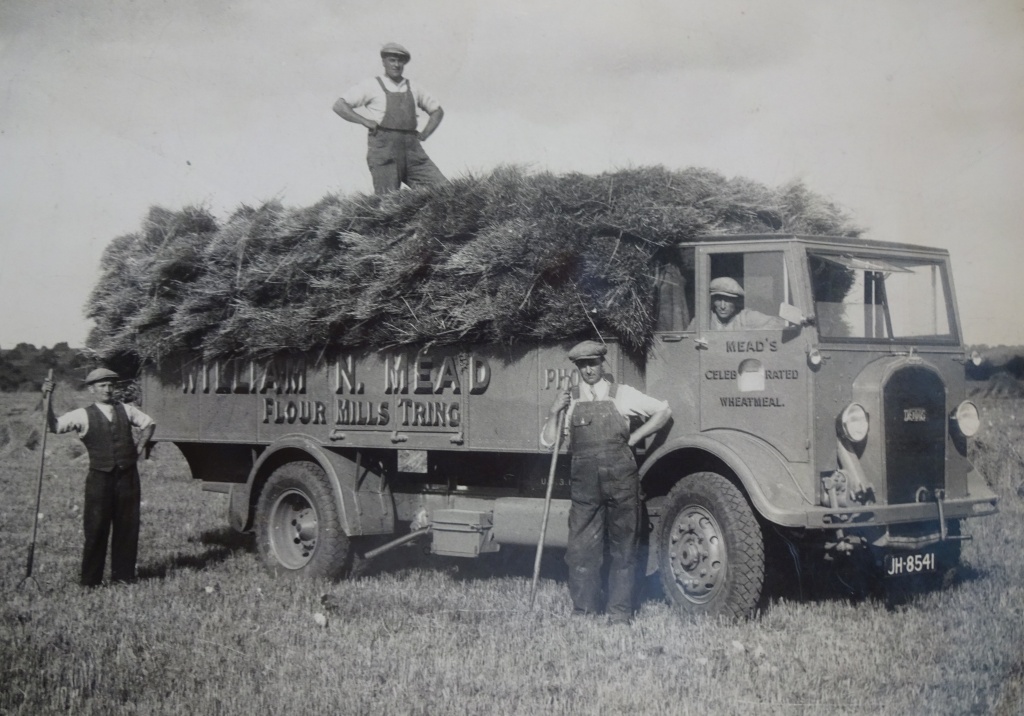
By the time this photo was
taken the steamers appear to have been replaced
by internal combustion-engined
vehicles. This is a Dennis dropside lorry c.1935.
According to a 1953 article appearing in the Berkhamstead Gazette, the fleet
then consisted of two 6-ton and three seven-ton Bedfords, a Foden lorry and trailer with a carrying capacity 15
tons, and a bulk grain wagon with a carrying capacity of 13 tons
used for haulage of wheat from the Docks. The article goes on
to say that
“even
this is insufficient to cope with the work, so that a large tonnage
of business is hauled by local contractors,”
a situation that continues.
Today, the mill is owned by Heygates Ltd., whose transport division
operate a fleet of 80 vehicles covering their three milling
operations (16 being based at Tring) to deliver 450,000 tons of
flour annually.
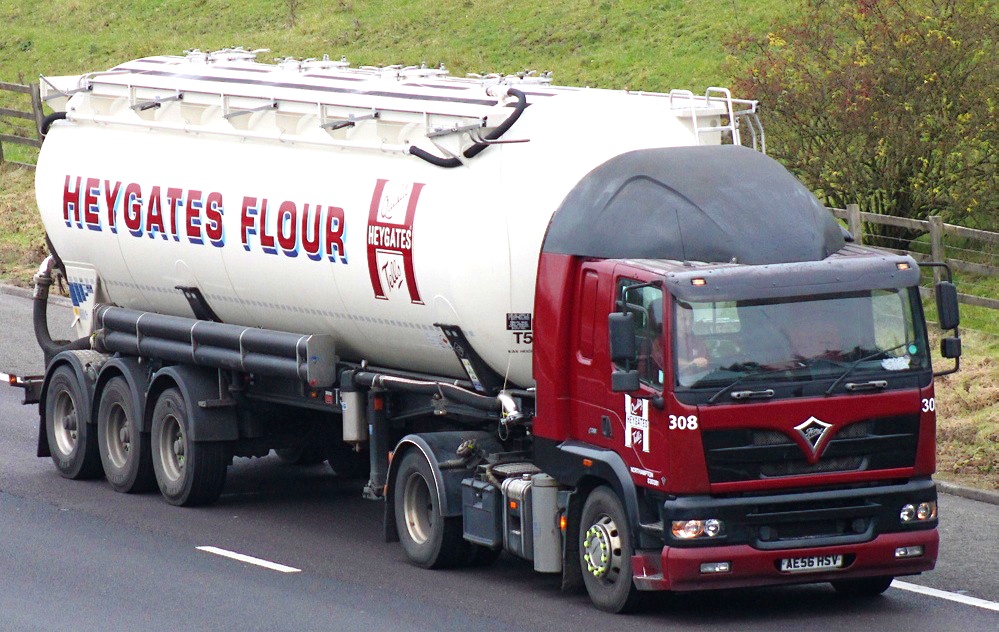
――――♦――――
THE BUSHELL BROTHERS’ BOATYARD
|
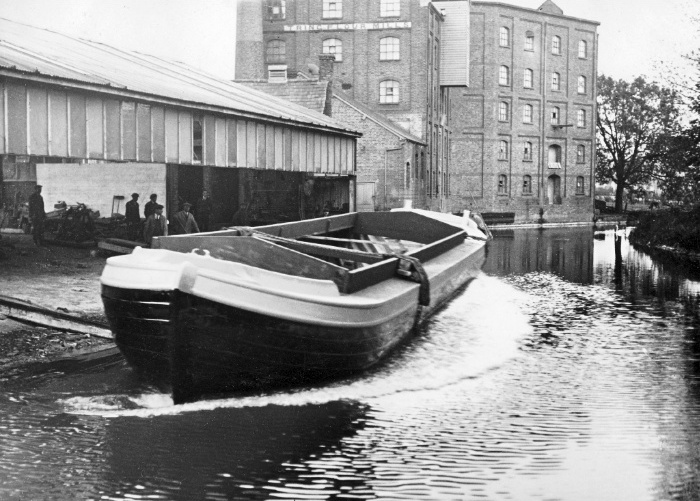
The
motor barge Progress being launched at Tring boatyard in 1934.
Until the 1940s, all the imported wheat and flour used for admixture
were carried along the Grand Junction Canal by barge from the London
Docks, and considerable quantities of flour were also despatched by
canal boat from Tring to London, particularly to the Fulham and
Chelsea districts. In the early days of the Mill the barges
often returned to London carrying other cargoes including hay and
straw for use in the horse-powered Metropolis.
Meads had their own fleet of barges, and from about 1850 John Bushell, a local man, was employed by the Meads to
build and repair them. At that
time canal boats were often built in small boatyards run by a few
men and this applied at Gamnel Wharf, where the boat builders worked in the open air in
the most extreme weather. Eventually – c.1930 – the open-sided shed
shown above was erected to provide some shelter from the elements.
Modernisation at the mill in 1875 resulted in John Bushell’s son
Joseph leasing the boatyard and developing it into a separate
business, while continuing to meet the Meads’ requirements for
building and maintaining their canal craft.
In 1912,
Joseph Bushell’s two sons, Joseph junior and Charles, took over
the business. They renamed it Bushell Brothers, and boats for
many of the largest canal users in the country were built and
repaired in their boatyard. Their crowning achievement was the
400 h.p. barge tug Bess built in 1920 for use on the Thames. Following
her sideways
launch she was taken along the Grand Junction Canal from Tring to London.
Most careful precautions had to be taken before this could he done
to ensure that she would clear all the bridges on the route, and
scale models of the tug and the two bridges likely to give trouble
were built, which showed a clearance of just 2 inches – when Bess
at length reached them, the clearance was found to be exactly 2
inches!
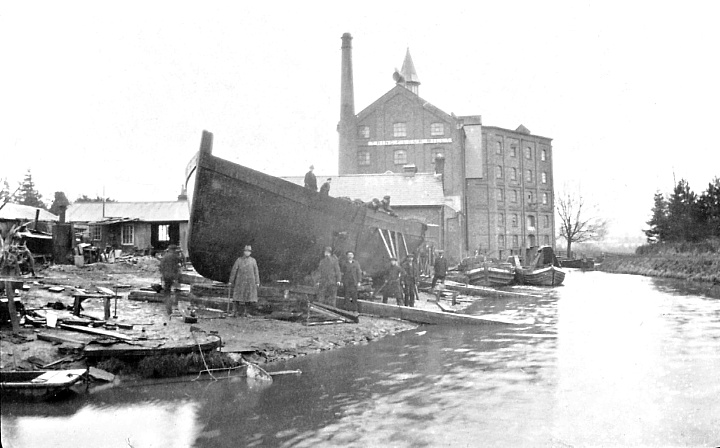
Bess being prepared at Bushell
Bros. boatyard for launching into the Wendover Arm at Gamnel.
Tring Flour Mill complete with
its splendid engine chimney is in the background.
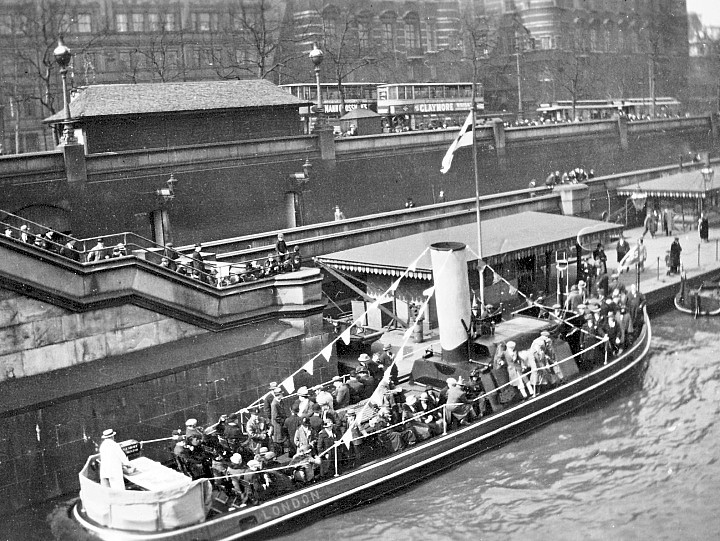
The Thames tug Bess, built
for the London Haulage Co. in 1920 by Bushell Bros. at Tring.
Originally powered by a 400 h.p.
steam engine, she was re-engined in 1926 with a 200 h.p.
Kromhout diesel.
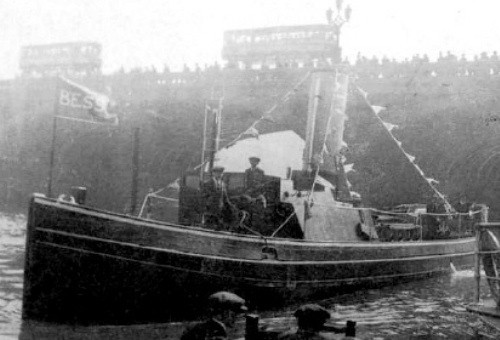
By the 1930s as
canal traffic and the market for new barges and repairs was declining,
and more varied work had to be sought.
Besides their work on narrowboats, the firm is known to have built
and repaired pleasure boats, maintenance flats, wide boats, tugs and
even a fire float, while their letterhead advertised boats for hire,
carpentry and decorating services.
Shortly before its closure in 1952, Bushells were constructing and
painting coachwork for commercial vehicles.
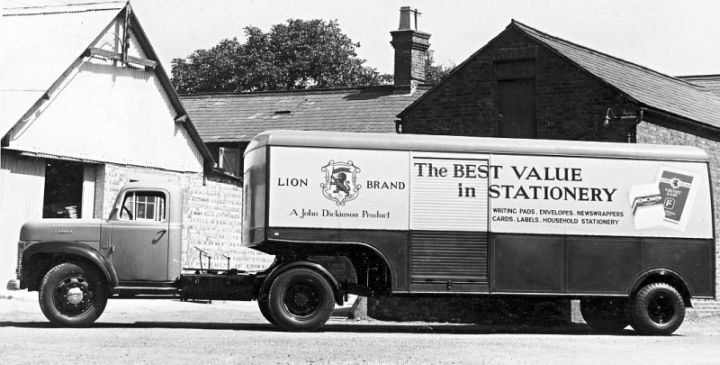
Some examples of Bushell Bros.
coachwork.
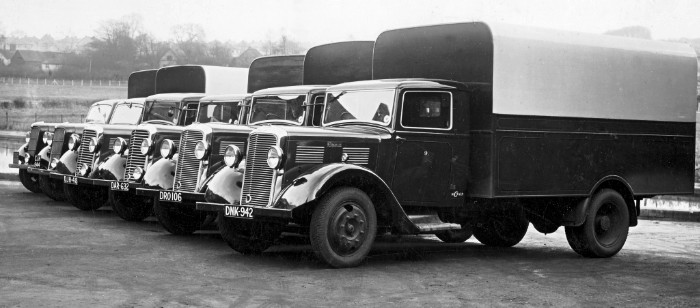
|
――――♦――――
TRING (HEYGATES) FLOUR MILL TODAY

Silos at Tring Flour Mill, from
the works entrance.
Today, flour milling continues at Gamnel Wharf, but in a manner
greatly transformed from its wind and steam-driven milling days.
The mechanical shafts, cogs, belts and sets of grindstones have long
been replaced by banks of cabinets that house sophisticated filters
and grinding rollers serviced by a network of pneumatic feeder
pipes. The finished product is no longer packed in the
2½ hundredweight (280 lbs.) sacks that carters like
William Massey had to deliver into bakers’ lofts, sometimes carrying
each sack up slippery external wooden steps or ladders. Today, Gamnel’s modern automated packing plant fills 32 kilos (70 lbs.)
sacks as well as a large output of 1½ kilo bags for the domestic
consumer market. These are then neatly palleted, swathed in polythene sheet,
and loaded onto lorries by forklift truck. Some flour also
leaves the mill in bulk transporters such as that shown on the right
of the picture above.
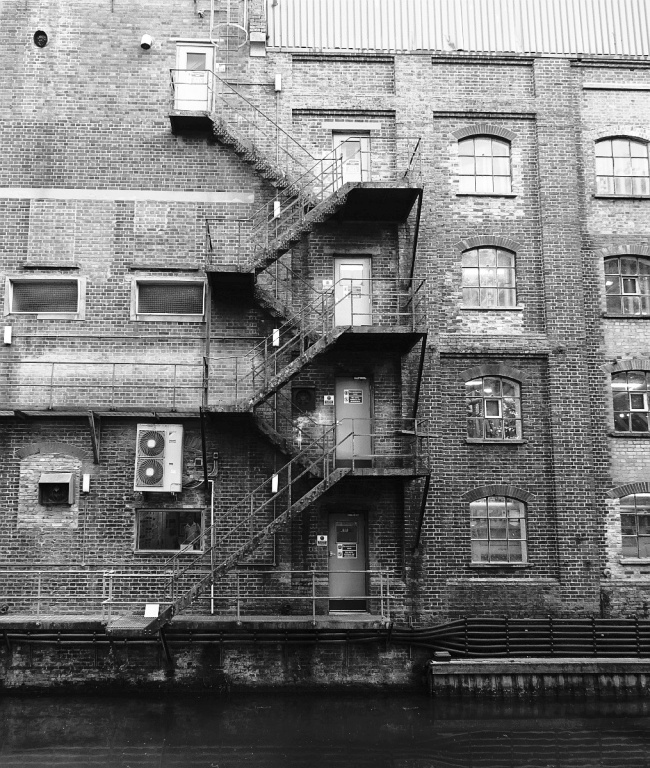
Rear of the steam mill of 1875.
In the days of the windmill, two millers could process half a ton of
grain per hour. Today, only two men are needed to operate the
plant, but its electrically-driven machinery operating under
computer control can mill 12 tons per hour; or put another way,
100,000 tons of wheat is milled in a year resulting in 76,000 tons
of flour (the bulk of the waste going into animal feed), mainly for
baking, but there is also a major commitment to wholemeal for
biscuits and bulk outlets. The mill employs a workforce of 80, and 16 trucks deliver its
products to outlets throughout the south of England.
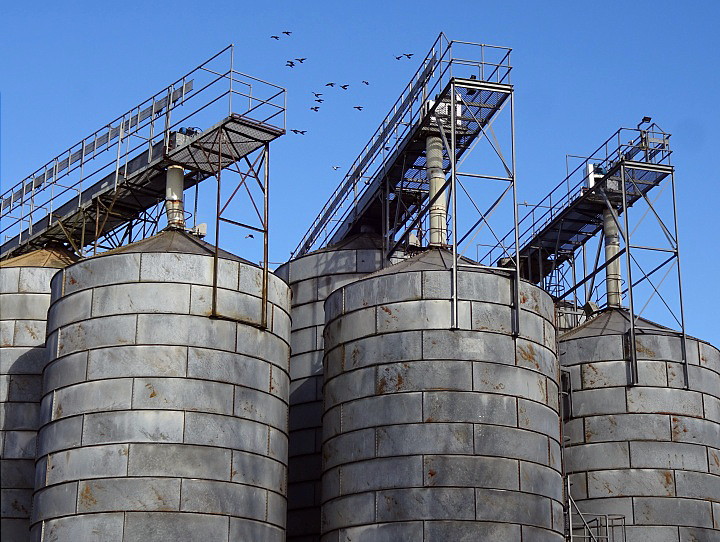
Silos
at the rear of the mill.
Overall, the Heygate Group spans farming, flour and feed milling and
baking, with seven flour mills on three sites, a feed mill, two
modern bakeries and 7,500 acres of mainly arable land in England.
In total it employs over 900 staff, compared to just 20 in 1935. Its
seven flour mills over three sites consume more than 450,000 tons of
wheat a year, the vast majority coming from British farms.
More than 80 grades of flour are produced, for breads, cakes,
pizzas, burger buns, chapattis, biscuits and more besides, supplying
large manufacturing plants, in-store supermarket bakeries and craft
bakers, delivering 24/7.
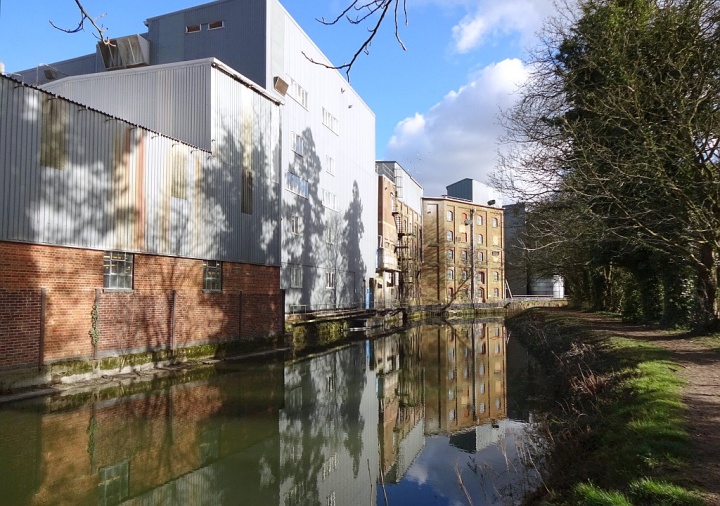
Rear of the flour mill from the Wendover Arm.
――――♦――――
APPENDIX 1
Before the actual milling process began, wheats were blended into
what was called the grist. The foot of each storage bin had a
calibrated release on a ratchet principle so that this could be set
and the correct quantity of each wheat released. All the wheats
contained extraneous matter to some extent, so the next process was
to remove this by a most exhaustive cleaning process, so that sound
grain, free from all impurities, resulted. By various elevators this
was then fed into a washing process, and from there into a
screen-meshed whizzer, to remove excess moisture.
The next process was to feed it into a heated container to open the
pores of the skin of the wheat, and then on to a cold container to
close the pores up again. The grist was then put into a conditioning
bin for 24 hours, with the result that drier grain absorbed moisture
from the damper, and a level moisture of about 16% was arrived at,
ready for the milling process.
The strongest gluten cells of the grain are towards the outer skin,
so the object of the treatment is to scrape them free without
breaking up the outer skin. A series of chilled steel spiral rolls
were employed, the first with serrations of four to the inch, the
top one of two revolving at a differential speed of 2 to 1, thus
opening the grain wide with a shearing action. The subsequent rolls
were serrated progressively less acutely. The release from these was
elevated to the top storey of the mill into a most ingenious machine
called a plansifter. This consisted of an outer wood casing
containing no less than 12 sieves, from a coarse wire mesh at the
top to a fine one at the bottom. The whole plansifter was suspended
from the ceiling attached to 16 flexible bamboo rods. Under the
bottom was an elliptical weight which, when in motion, afforded a
perfect sieving motion.
The releases from this operation were fed back to the roller floor,
the coarsest to the second rolls, and according to the grading, to
each appropriate roll, and a final pair of smooth rollers. Meanwhile, the finer separations from the plansifter were fed to the
enclosed cylinders inclined at an angle but clothed with coarsely
meshed cloth. The finer release was then fed to the next machine
clothed with finer mesh, and the over-tail despatched to the last
sequence of the rolls.
The resultant fine release was now actual flour, which was fed to a
holding bin, from where it was bagged up by an operative into jute
bags weighing 140 lbs. nett. (Nowadays it is packed into 32 kgs.
stiff paper bags, or alternatively stored in a glass-lined bin, from
which it is loaded into bulk lorries, and at the bakeries blown from
the lorries by means of compressed air into the bakers’ bins.)
――――♦――――
APPENDIX 2
In 1898, William Mead acquired Tring Flour Mill from his
father in exchange for an annuity of £200 p.a. Being a prudent
businessman, before completing the transaction William arranged to
have the business valued to assess whether it was worth the
capitalised cost of the annuity in relation to his father’s likely
lifespan (Thomas was then 65). |
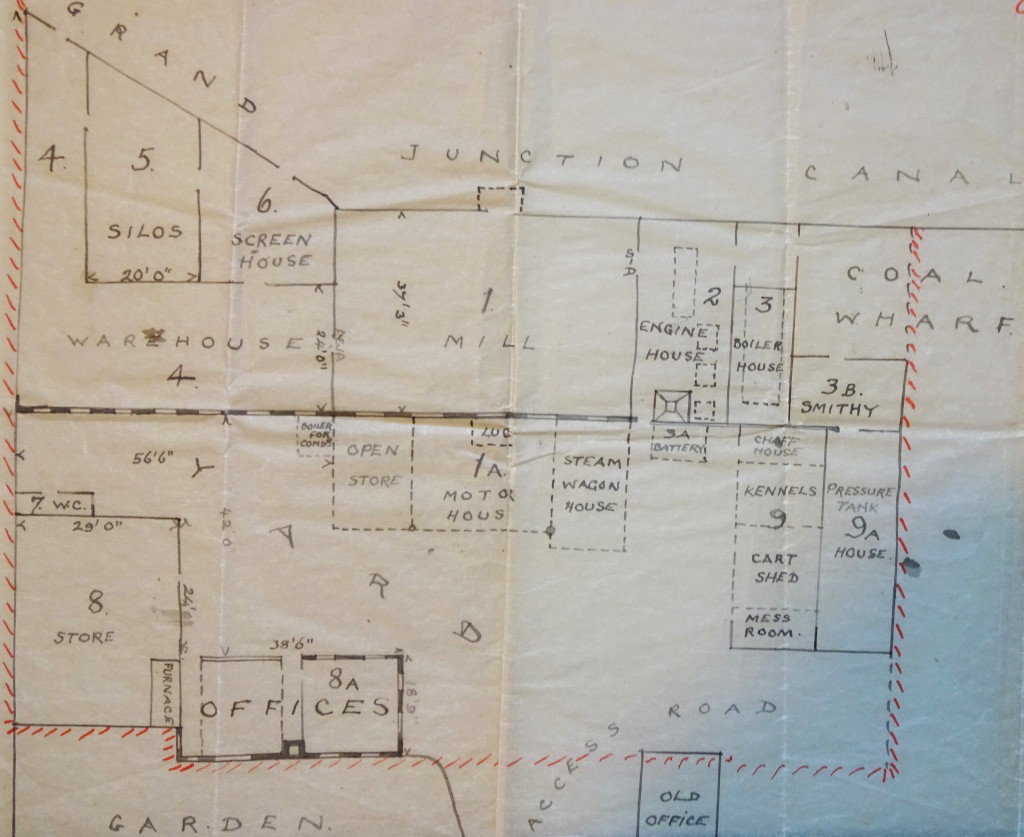
This plan of the mill in 1929
was found among
some Mead family papers.
The
valuation has disappeared, but the following manuscript letter that
accompanied it provides an
interesting summary of the fixed assets of the business as they then
existed:
“In accordance with your instructions I have attended at the Steam
Flour Mills, Tring, July 5/98 and now beg to make the following
remarks.
The property consists of (all being freehold) a brick built
and slated house, fronting the Wingrave Road, containing kitchen,
scullery, dining room with marble mantel & folding doors to garden,
small sitting room with grate, passage & small wine cellar off;
basement and cellar.
First Floor: five bedrooms, bathroom and W.C.
There are also two staircases.
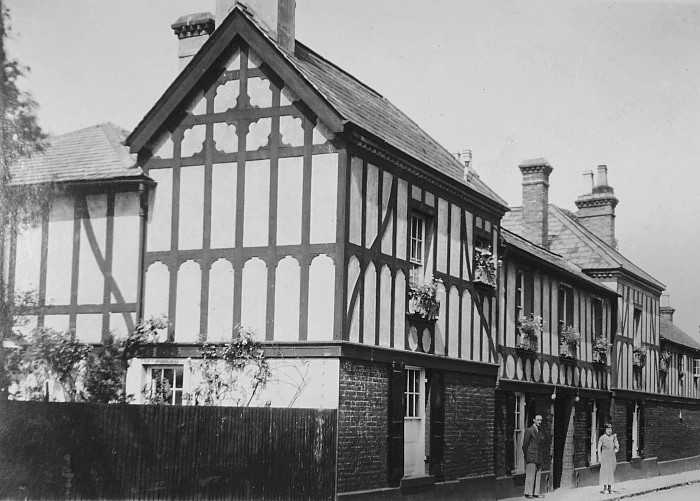
The Mill House, c.1930s.
Adjoining (and though originally a separate house, it is now
connected) is a brick built and slated dwelling house containing, in basement,
a dairy and cellar: ground floor, washhouse with 2 coppers, with range
and cupboards.
Room with grate forming entrance hall (under staircase is entrance
to a cellar), drawing room with marble mantel, dining room, also
entered from garden is a small office up steps.
In the rear is a pretty garden, tastefully laid out with shrubs,
trees, grass plots and paths.
The construction of the above mentioned houses is somewhat peculiar. They were originally a row of cottages, which have been built onto
and converted into their present state. The condition and state of
repair is generally speaking very satisfactory. Both houses are
inhabited by Mr Thomas Mead and his family.
Crossing the Wingrave Road, I came to a nice enclosure of a paddock,
enclosed with brick walls on two sides and containing a tennis
court, nut stems and fruit trees. At one side and at one time forming
part of same is a capital garden, enclosed with a high wall and well
stocked with fruit trees and laid out with paths. In it are a lean
to potting house and two lean two vineries.
The above described freehold land contains about 1½ acres. It has a
long frontage to the Wingrave Road and forms an excellent building
site. I understand, however, that at the present time there is no
demand for ground for such a purpose here.
Again crossing the road, I come to the wharf and business premises
connected with the mill, including four freehold brick built and
slated cottages, containing two rooms upstairs and two rooms
downstairs. Range of brick and slated wood barns to each house, also 2
WCs and shed at end. These cottages are substantially built and in a
very fair state of repair. They are let at 2s 6d per cottage per
week, the landlord paying outgoings.
Also abutting onto the Wingrave Road is a range of brick built and
slated stables and coach house (4 stall stable), also loose box, nag
stable and harness room. The coach house is entered by double
folding gates. The whole has lofts over.
In the rear of above is a range of brick built and tiles pigsties
with enclosed yard, 2 pigsties, feeding place and yard at back, and
open cast shed. Further is a paved washhouse with copper, 2 sinks
and 2 pumps with loft over brick built and slated coach house with
folding gates and loft over. Part paved yard behind. Boarded and
tiled 5 stall stable with brick underpinning and paved. Attached and
forming part of above is open shed, and oil shed.
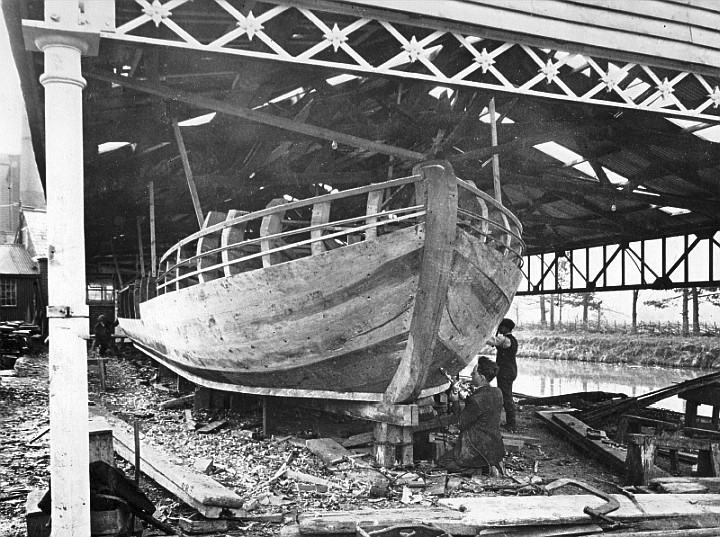
The boat-building business that in
1912 became Bushell Bros.
There is also the spacious wharf used as a boat building
establishment and occupied by Messrs W. Mead and Co. Ltd., who have
erected several sheds for the carrying out of the business, which
are their property. The wharf also contains, adjoining the canal a
part brick built, boarded and slated warehouse and store with lofts;
also a brick built and slated warehouse further; a boarded warehouse
on brick underpinning with pan tile roof; a long boarded shed with
galvanised iron roof; a brick built and slated building forming a
forge and workshop.
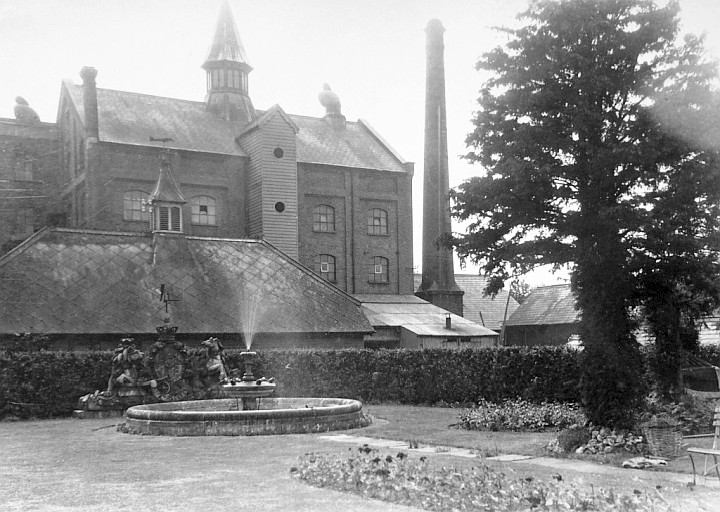
The flour mill viewed from the
owner’s garden, engine and boiler house on the right.
William Mead bought
the ornamental fountain at the dispersal sale of Aston Clinton House
in 1923, while the stone relief coat-of-arms behind it
came from the Mark Lane Corn Exchange in London when it was
demolished in 1931.
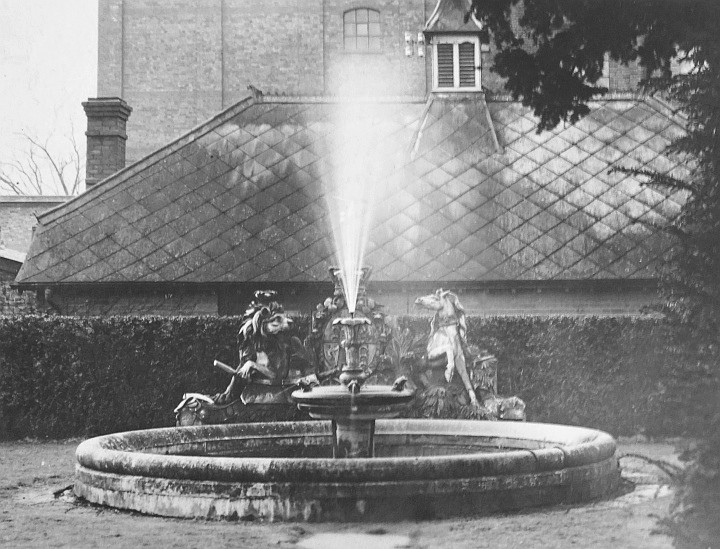
The modernly substantially brick built slated steam flour mill,
known as Tring Steam Flour Mill. This is a very imposing and
handsome building erected as recently as 1875. It comprises a
lean-to boiler house and shaft through door to engine room.
The mill consists of five spacious and lofty floors fitted with
necessary bins. Above top floor is a platform and above a
glazed observatory. Boats can be loaded or unloaded directly
from, or to the mill ex canal. In front of the mill and
setting off the appearance is a very useful ornamental iron built
loading shed, which has recently been erected at a considerable
cost.

Edith
Mead and her three daughters in
the Mill House garden (one daughter died in childhood)
At right side of mill is a brick built and slated cart shed, chaff
house and 2 stall stable, loft over. On left hand is a
recently erected open shed with galvanised iron roof. Also a
weighing office and weigh bridge.
Adjoining, and entered by a covered passage from the modern mill, is
the original 4 story windmill in going order and repair, with a
lean-to brick built and slated store surrounding the base.
Part boarded and brick built store in position of old mill
adjoining. Brick built and slated engine room now used as a
wagon shed.”
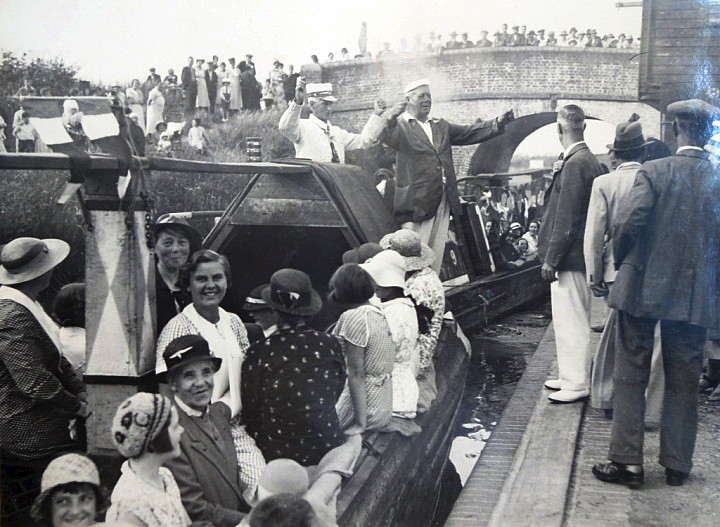
A Sunday School outing about to
depart from Tring Flour Mill in 1931.
William Mead is shown with his arms outstretched.
――――♦――――
FOOTNOTES
1. Yes, the shareholders of Thames Water would
classify sewage disposal as a ‘business’, even if their works at
Gamnel has not exactly been a profit centre in recent times (a fine of £1m plus costs was imposed on Thames Water
in January 2016 for discharging partially treated sewage from its Gamnel
sewage works into
the adjacent Wendover Arm of the Grand Union Canal).
2. Advertisements suggest that the sale of coal at Gamnel Wharf
continued to be
a lucrative business until government restrictions brought it to an
end at the outbreak of
World War II.
3.
The Wheat Act 1932 aimed to provide U.K. wheat-growers with a secure
market and enhanced prices for home-grown wheat of millable quality.
4.
“At one time the
chief officer at Cambridge was a fiend of a bureaucrat, and every
pettifogging little detail of the regulations had to be conformed
to. On one occasion I had an excess of 28 lbs. of face value on the
coupon returns I submitted, and my ‘friend’ at Cambridge refused to
accept other than an exact balance on the forms, and sent the
offending one back. I telephoned him, explaining the difficulties
in getting a balance to the exact pound every time, but he still
said he would refuse to accept, so I said
‘Right, then, I shall just
blot out the quarter of a hundredweight, and re-submit.’
I was
immediately told this would be an offence!
Hinting
that I had a friend in high office at the Ministry, I called his
bluff and got my Buying Permits.” . . . . Taken from Ralph
Seymour’s
autobiographical note.
5. The other shareholders were William’s wife Edith
– she being the majority shareholder – and his two daughters.
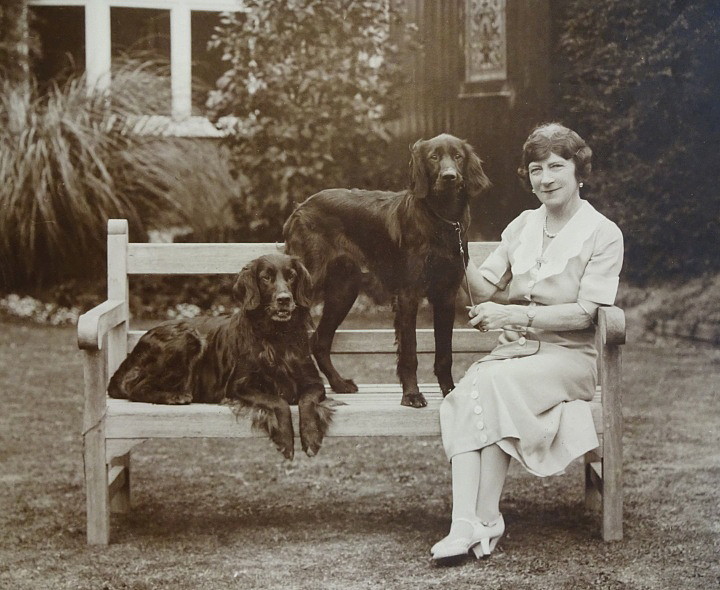
Edith Mead, c.1930s.
6. The first mill on the site was established in
800 AD and, by the time of the Domesday Book, was the third-highest rated mill in England.
It is now the site of the Heygate Group’s
headquarters and its flour mill, whose large central tower can be
seen for several miles around.
7. The National Loaf was of bread made from wholemeal flour with added
calcium and vitamins. Introduced by the government in 1942 to
save space in shipping wheat to Britain, the loaf was made from
wholemeal flour to combat wartime shortages of white flour.
The bread was grey, mushy and unappetising, and contained quite a
high amount of salt to make it keep longer - only one person in
seven preferred it to white bread. In 1950 sliced, wrapped
white loaves were again allowed to be sold, which people preferred,
although the National Loaf was not discontinued until October 1956. |
――――♦――――
<> >
|